Em 2025, o mercado de máquinas de perfuração está crescendo, impulsionado por avanços tecnológicos e crescente demanda industrial. Este artigo fornece uma análise aprofundada dos principais fatores de seleção, incluindo especificidade da aplicação, especificações da máquina e considerações de custo. Ele oferece orientação valiosa para compradores profissionais na tomada de decisões informadas, garantindo desempenho e lucratividade ideais.
Sumário:
- Visão geral do mercado de máquinas de perfuração
-Introdução e análise detalhadas do mercado de máquinas de perfuração
- Fatores-chave ao selecionar uma máquina de perfuração
- Inovações em tecnologia de máquinas de perfuração
-Considerações ambientais nas operações de máquinas de perfuração
- Tendências futuras em tecnologia de máquinas de perfuração
-Encerrando
Visão geral do mercado de máquinas de perfuração
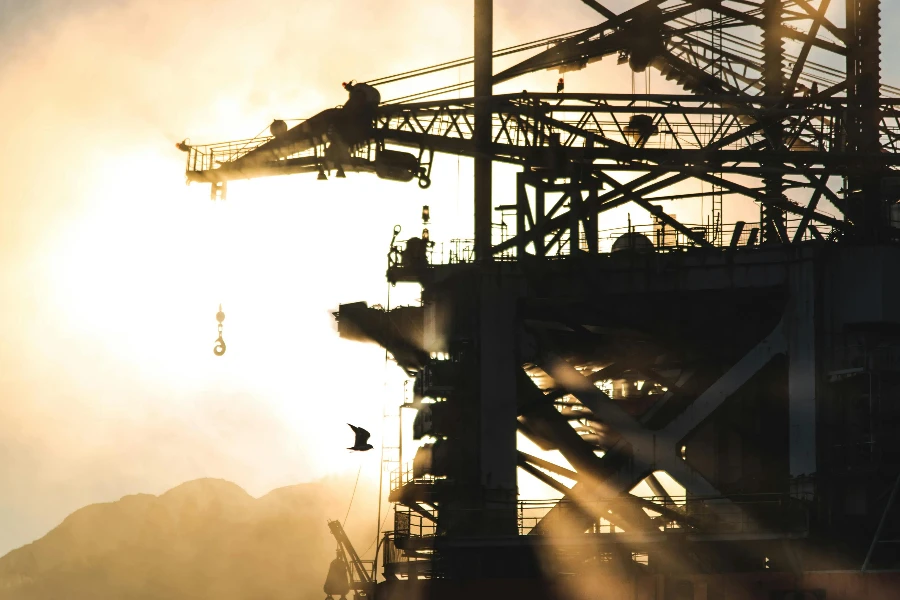
O mercado global de máquinas de perfuração tem visto um crescimento significativo nos últimos anos. Em 2023, o mercado valia aproximadamente US$ 4.4 bilhões e está projetado para atingir US$ 6.2 bilhões até 2030, crescendo a um CAGR de 5.0%. Esse crescimento é impulsionado por avanços em tecnologias de fabricação e aumento da demanda de indústrias como automotiva, aeroespacial e máquinas pesadas. Espera-se que o segmento de uso final de transporte veja o crescimento mais substancial, atingindo US$ 2.9 bilhões até 2030 com um CAGR de 5.3%, enquanto o segmento de máquinas gerais deve crescer a um CAGR de 4.4%.
Regionalmente, o mercado dos EUA foi estimado em US$ 1.2 bilhão em 2023, e o mercado da China deve crescer a um impressionante CAGR de 7.6%, atingindo US$ 1.4 bilhão até 2030. Outros mercados significativos incluem Japão, Canadá, Alemanha e a região mais ampla da Ásia-Pacífico, todos os quais devem contribuir para o crescimento geral do mercado de máquinas de perfuração.
Introdução e análise detalhadas do mercado de máquinas de perfuração
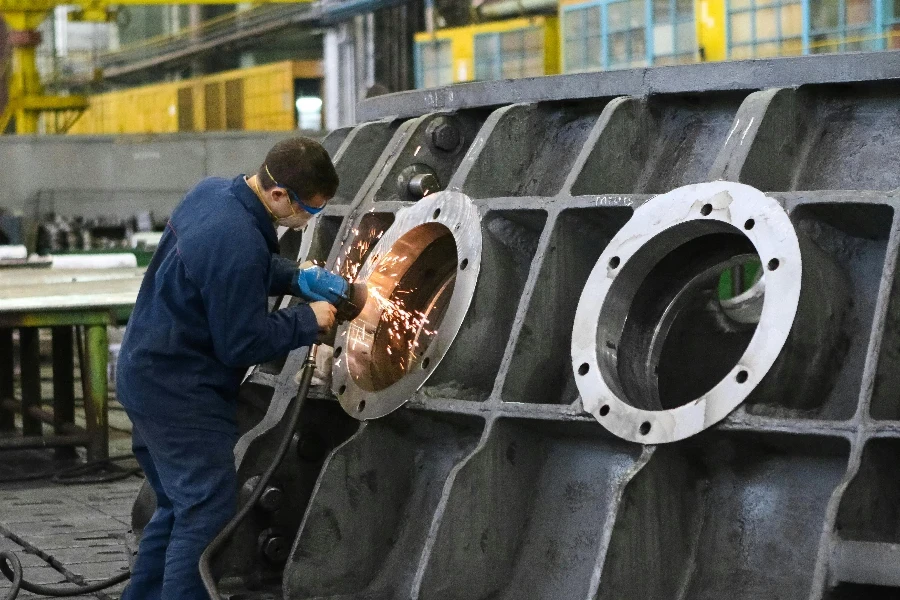
As máquinas de mandrilar são cruciais na usinagem de precisão, particularmente em indústrias que exigem alta precisão e acabamentos suaves, como automotiva, aeroespacial e máquinas pesadas. Essas máquinas são projetadas para ampliar e finalizar furos pré-perfurados ou fundidos com alta precisão, garantindo que o diâmetro, o acabamento da superfície e a tolerância atendam às especificações exatas. O mercado é segmentado em tipos de mandrilamento fino e mandrilamento bruto, cada um atendendo a diferentes necessidades com base no material e nas condições de corte.
Os avanços tecnológicos melhoraram significativamente o desempenho e a versatilidade das máquinas de mandrilar. Inovações como revestimentos e materiais avançados para arestas de corte, incluindo diamante policristalino (PCD) e nitreto cúbico de boro (CBN), oferecem resistência superior ao desgaste e maior vida útil da ferramenta. Além disso, cabeçotes de mandrilar controlados digitalmente permitem ajustes em tempo real durante a usinagem, fornecendo precisão incomparável e reduzindo erros. A integração da tecnologia de sensores para manutenção preditiva otimizou ainda mais o processo de usinagem e reduziu o tempo de inatividade.
Apesar desses avanços, o mercado de máquinas de perfuração enfrenta desafios. Manter a precisão em uma ampla gama de materiais, gerenciar a geração de calor e abordar a tendência de miniaturização em indústrias como eletrônicos e dispositivos médicos são problemas contínuos. Os fabricantes estão explorando técnicas avançadas de resfriamento e desenvolvendo ferramentas mais robustas e versáteis para abordar esses desafios. As pressões de custo na fabricação também impulsionam a necessidade de máquinas de perfuração mais eficientes que possam oferecer alto desempenho, minimizando o tempo de inatividade e o desperdício.
Fatores-chave ao selecionar uma máquina de perfuração
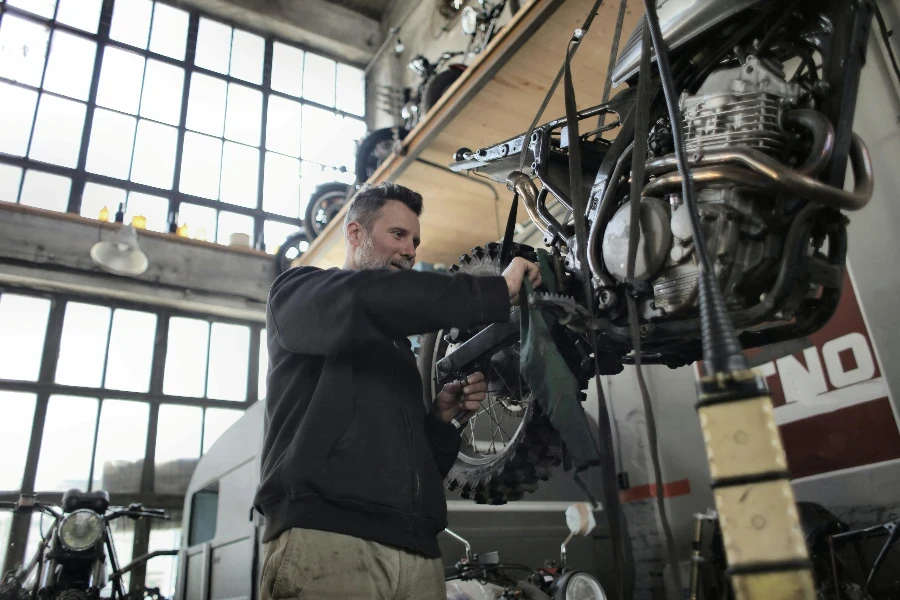
Especificidade do aplicativo
Ao selecionar uma máquina de perfuração, o primeiro fator a considerar é a aplicação específica para a qual ela será usada. Diferentes máquinas de perfuração são projetadas para lidar com tarefas variadas, como perfuração de precisão, perfuração por gabarito, perfuração por torno, perfuração vertical e perfuração horizontal. Por exemplo, máquinas de perfuração de precisão são ideais para produzir superfícies cilíndricas internas altamente precisas, enquanto máquinas de perfuração por gabarito são adequadas para criar furos com dimensões e localizações precisas. Entender os requisitos específicos da tarefa ajudará na escolha do tipo de máquina apropriado.
As máquinas de perfuração de precisão normalmente usam operações de corte de ponto único para atingir precisão dentro de ±0.0001 polegadas, tornando-as adequadas para tarefas de alta precisão, como acabamento de superfícies de rolamentos internos. Em contraste, as máquinas de perfuração horizontais, que podem lidar com peças maiores e oferecem recursos multifuncionais, como fresamento e perfuração, são melhores para aplicações pesadas que exigem versatilidade.
A complexidade da peça de trabalho, as tolerâncias necessárias e o material em que está sendo trabalhado são considerações críticas. Por exemplo, materiais com dureza mais alta, como aço inoxidável, podem necessitar de máquinas equipadas com ferramentas de carboneto ou diamante para manter a precisão e a eficiência.
Especificações da máquina
As especificações técnicas de uma máquina de perfuração são essenciais para garantir que ela atenda às demandas de sua aplicação. As principais especificações incluem velocidade do fuso, taxa de avanço, velocidade de corte e a potência da máquina. A velocidade do fuso, medida em revoluções por minuto (RPM), determina a rapidez com que a ferramenta de corte gira e pode afetar a qualidade do acabamento e a eficiência do processo de usinagem. Velocidades mais altas do fuso são normalmente necessárias para acabamentos mais finos e materiais mais duros.
A taxa de avanço, geralmente medida em polegadas por minuto (IPM), indica a taxa na qual a ferramenta de corte avança no material. Um equilíbrio adequado entre a velocidade do fuso e a taxa de avanço é crucial para evitar o desgaste da ferramenta e atingir o acabamento de superfície desejado. A velocidade de corte, a velocidade na qual a aresta de corte da ferramenta se move ao longo da superfície da peça de trabalho, também desempenha um papel significativo na determinação da eficiência e qualidade do processo de mandrilamento.
Os requisitos de potência da máquina, geralmente especificados em cavalos de potência (HP), devem estar alinhados com a taxa de remoção de material e a dureza do material sendo usinado. Por exemplo, máquinas de perfuração que trabalham com materiais como aço inoxidável e ferro fundido, que têm requisitos de potência unitária mais altos, precisarão de motores mais potentes para manter o desempenho.
Tolerância e Precisão
Tolerância e precisão são fatores críticos na seleção de uma máquina de mandrilar, especialmente para aplicações que exigem alta precisão. A tolerância de uma máquina de mandrilar se refere ao desvio permitido das dimensões especificadas, que pode variar dependendo do tipo de máquina e da aplicação. Máquinas de mandrilar de precisão, por exemplo, podem atingir tolerâncias tão apertadas quanto ±0.0001 polegadas, tornando-as adequadas para aplicações onde a precisão dimensional é primordial.
Condições ambientais, geometria da ferramenta e o alinhamento dos componentes e fixações da máquina também influenciam a precisão do processo de mandrilamento. Usar fluidos de corte pode ajudar a manter a temperatura da ferramenta, reduzir o desgaste e permitir maiores velocidades de corte e taxas de avanço, aumentando assim a precisão.
Além disso, a rigidez da máquina, da peça de trabalho e da configuração da ferramenta é crucial para manter a precisão durante o processo de perfuração. Máquinas com construção robusta e componentes de alta qualidade têm menos probabilidade de sofrer deflexão ou vibração, o que pode comprometer a precisão.
Compatibilidade de Material
A compatibilidade da máquina de mandrilar com diferentes materiais é outra consideração importante. Ferramentas de mandrilar são tipicamente feitas de aço rápido (HSS), carboneto, cerâmica ou diamante, cada um adequado para diferentes materiais e aplicações. Por exemplo, ferramentas de carboneto e diamante são preferidas para usinar materiais duros como aço inoxidável, enquanto ferramentas HSS são adequadas para materiais mais macios como alumínio e latão.
Entender as propriedades do material, como dureza e usinabilidade, é essencial para selecionar a máquina de perfuração e as ferramentas certas. Por exemplo, materiais com altos valores de dureza, como ferro fundido e aço inoxidável, exigem ferramentas com maior resistência ao desgaste e velocidades de corte para manter a eficiência e a precisão.
Além disso, a escolha do fluido de corte pode impactar o processo de usinagem, particularmente ao trabalhar com materiais que geram calor significativo. Os fluidos de corte ajudam a reduzir o desgaste da ferramenta, melhoram o acabamento da superfície e aumentam as velocidades de corte, tornando-os um componente vital em operações de mandrilamento.
Custo e orçamento
Por fim, o custo e o orçamento para aquisição de uma máquina de perfuração devem ser considerados. As máquinas de perfuração variam significativamente em preço com base em seu tipo, especificações e recursos. Máquinas de perfuração automatizadas e controladas por CNC, que oferecem maior precisão e eficiência, tendem a ser mais caras do que máquinas manuais ou semiautomáticas.
O investimento em uma máquina de perfuração deve estar alinhado com o retorno esperado sobre o investimento (ROI) e as necessidades específicas da operação. Para operações de pequena escala ou menos frequentes, uma máquina de menor custo com recursos básicos pode ser suficiente. No entanto, para produção de alto volume ou aplicações que exigem alta precisão, investir em uma máquina mais avançada e cara pode resultar em economia de custos a longo prazo por meio de eficiência aprimorada e tempo de inatividade reduzido.
Custos de manutenção, substituição de ferramentas e consumo de energia também devem ser considerados no orçamento geral. Máquinas com maior eficiência energética e menores requisitos de manutenção podem reduzir significativamente os custos operacionais ao longo do tempo.
Inovações em tecnologia de máquinas de perfuração
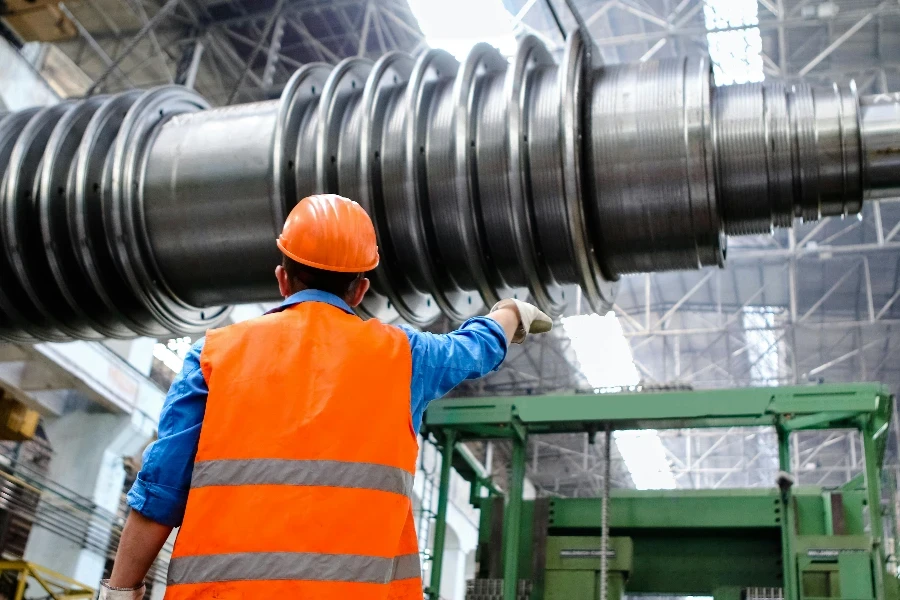
Integração CNC
A integração da tecnologia de Controle Numérico Computadorizado (CNC) em máquinas de mandrilar revolucionou a indústria ao aumentar a precisão, eficiência e automação. As máquinas de mandrilar CNC são programadas usando código G, permitindo controle preciso sobre o movimento, velocidade e taxa de avanço da ferramenta de corte. Essa tecnologia permite que tarefas complexas e repetitivas sejam realizadas com intervenção humana mínima, reduzindo a probabilidade de erros e aumentando a produtividade.
As máquinas de mandrilar CNC podem ser equipadas com recursos avançados, como trocadores automáticos de ferramentas, que permitem o uso de várias ferramentas em uma única operação sem intervenção manual. Essa capacidade é particularmente benéfica para aplicações que exigem diferentes ferramentas de corte para vários estágios do processo de mandrilamento, como desbaste e acabamento.
Além disso, a tecnologia CNC facilita o uso de software de simulação para modelar o processo de perfuração antes da usinagem real, identificando problemas potenciais e otimizando parâmetros para eficiência e precisão aprimoradas. Essa capacidade preditiva reduz os tempos de configuração e minimiza o desperdício de material, contribuindo para economia de custos e sustentabilidade ambiental.
Materiais de ferramentas avançadas
O desenvolvimento de materiais de ferramentas avançadas impactou significativamente o desempenho e a durabilidade das máquinas de perfuração. Materiais de alto desempenho, como diamante policristalino (PCD) e nitreto cúbico de boro (CBN), oferecem dureza e resistência ao desgaste superiores em comparação às ferramentas tradicionais de HSS e carboneto. Esses materiais permitem maiores velocidades de corte, maior vida útil da ferramenta e melhores acabamentos de superfície, principalmente ao usinar materiais duros e abrasivos.
Ferramentas de PCD são ideais para materiais não ferrosos, como alumínio e compósitos, fornecendo alta precisão e vida útil estendida. Ferramentas de CBN, por outro lado, são adequadas para materiais ferrosos, como aço temperado e ferro fundido, oferecendo excelente estabilidade térmica e resistência ao desgaste.
O uso de revestimentos avançados, como nitreto de titânio (TiN) e óxido de alumínio (Al2O3), melhora ainda mais o desempenho da ferramenta ao reduzir o atrito e a geração de calor durante o processo de corte. Esses revestimentos melhoram a evacuação de cavacos, reduzem o desgaste da ferramenta e permitem maiores velocidades de corte, resultando em maior produtividade e economia de custos.
Automação e Robótica
Automação e robótica estão desempenhando um papel cada vez mais importante na indústria de máquinas de perfuração, aumentando a eficiência, precisão e segurança. Máquinas de perfuração automatizadas podem executar tarefas complexas com intervenção humana mínima, reduzindo custos de mão de obra e o risco de erros. Sistemas robóticos podem ser integrados com máquinas de perfuração para automatizar o manuseio de materiais, trocas de ferramentas e inspeções de qualidade, simplificando ainda mais o processo de fabricação.
Por exemplo, braços robóticos podem carregar e descarregar peças de trabalho, posicioná-las com precisão na máquina e executar operações secundárias, como rebarbação e limpeza. Esse nível de automação não só aumenta a produtividade, mas também melhora a segurança no local de trabalho, reduzindo a necessidade de manuseio manual de materiais pesados e perigosos.
Os sistemas robóticos também podem ser equipados com sensores avançados e algoritmos de aprendizado de máquina para monitorar o processo de perfuração em tempo real, detectando anomalias e fazendo ajustes para otimizar o desempenho. Essa capacidade aumenta a eficiência geral e a confiabilidade do processo de usinagem, reduzindo o tempo de inatividade e os custos de manutenção.
Considerações ambientais em operações de máquinas de perfuração
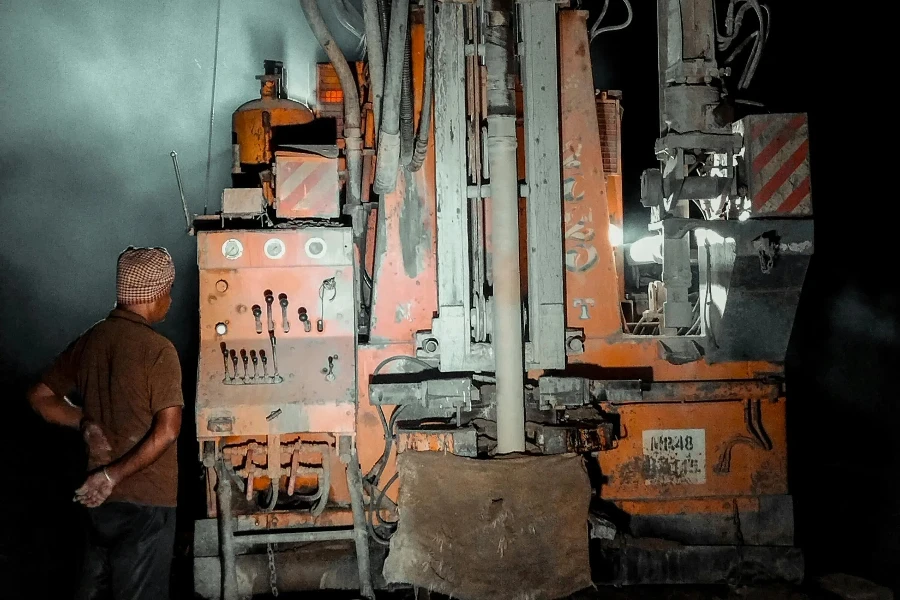
Eficiência energética
A eficiência energética é uma consideração crítica nas operações modernas de máquinas de perfuração, motivada pela necessidade de reduzir custos operacionais e impacto ambiental. Avanços na tecnologia de motores, como motores elétricos de alta eficiência e acionamentos de frequência variável (VFDs), melhoraram significativamente a eficiência energética das máquinas de perfuração. Essas tecnologias permitem controle preciso sobre a velocidade e o torque do motor, reduzindo o consumo de energia e otimizando o desempenho.
Além disso, o uso de componentes de eficiência energética, como iluminação LED e eletrônicos de baixo consumo, contribui ainda mais para a economia geral de energia. Implementar sistemas de gerenciamento de energia para monitorar e controlar o uso de energia em tempo real pode ajudar a identificar ineficiências e implementar medidas corretivas, resultando em economias substanciais de custos e redução da pegada de carbono.
Redução de residuos
A redução de desperdício é outro aspecto importante das operações sustentáveis de máquinas de perfuração. A utilização eficiente de material e os processos de usinagem otimizados podem minimizar o desperdício de material e reduzir o impacto ambiental da fabricação. O software de simulação avançado e a tecnologia CNC permitem controle preciso sobre o processo de perfuração, reduzindo as taxas de refugo e melhorando o rendimento do material.
Reciclar e reutilizar fluidos de corte, cavacos e outros materiais residuais também pode contribuir para a redução de resíduos. Implementar sistemas de circuito fechado para gerenciamento de fluidos de corte e reciclagem de cavacos pode minimizar os custos de descarte de resíduos e reduzir o impacto ambiental das operações de usinagem.
Controle de emissão
Controlar as emissões das operações de máquinas de perfuração é essencial para manter um local de trabalho seguro e ecologicamente correto. O uso de sistemas avançados de filtragem, como coletores de névoa e purificadores de ar, pode capturar e remover efetivamente contaminantes transportados pelo ar, incluindo névoa de óleo, vapores de refrigerante e material particulado. Esses sistemas ajudam a manter a qualidade do ar e a cumprir com as regulamentações ambientais, protegendo a saúde dos trabalhadores e da comunidade ao redor.
Além disso, a seleção de fluidos de corte e lubrificantes ecologicamente corretos pode reduzir emissões prejudiciais e melhorar a segurança no local de trabalho. Fluidos de corte biodegradáveis e à base de água oferecem uma alternativa mais segura e sustentável aos fluidos tradicionais à base de óleo, minimizando o impacto ambiental das operações de usinagem.
Tendências futuras na tecnologia de máquinas de perfuração
Fabricação Inteligente
A ascensão da Indústria 4.0 e da manufatura inteligente está pronta para transformar a indústria de máquinas de perfuração, com maior conectividade, análise de dados e automação, impulsionando melhorias em eficiência e precisão. Máquinas de perfuração inteligentes equipadas com sensores e conectividade IoT podem coletar e analisar dados em tempo real, fornecendo insights valiosos sobre o desempenho da máquina, desgaste da ferramenta e parâmetros do processo.
Essa abordagem orientada por dados permite manutenção preditiva, reduzindo o tempo de inatividade e estendendo a vida útil de máquinas e ferramentas. Ao identificar problemas potenciais antes que eles levem a falhas de máquina, os fabricantes podem otimizar os cronogramas de manutenção e reduzir o risco de quebras inesperadas, melhorando a produtividade geral e a eficiência de custos.
Integração de Manufatura Aditiva
A integração da manufatura aditiva (AM) com processos tradicionais de mandrilamento oferece novas possibilidades para produção e personalização de peças complexas. Máquinas híbridas que combinam capacidades de manufatura aditiva e subtrativa podem produzir geometrias intrincadas e características internas que são difíceis ou impossíveis de serem alcançadas apenas com usinagem convencional.
A manufatura aditiva permite a criação de peças quase líquidas, reduzindo o desperdício de material e minimizando a necessidade de usinagem extensiva. Ao combinar AM com mandrilamento de precisão, os fabricantes podem obter acabamentos de alta qualidade e tolerâncias apertadas em peças complexas, expandindo a gama de aplicações e melhorando a eficiência geral.
Sustentabilidade e Economia Circular
A sustentabilidade e a economia circular estão se tornando cada vez mais importantes na indústria de manufatura, impulsionando o desenvolvimento de tecnologias de máquinas de perfuração mais ecologicamente corretas. Os fabricantes estão se concentrando em reduzir o consumo de energia, minimizar o desperdício e promover a reutilização e a reciclagem de materiais.
A adoção de práticas sustentáveis, como o uso de fontes de energia renováveis, a implementação de sistemas de circuito fechado para gerenciamento de fluidos de corte e o projeto de máquinas para fácil desmontagem e reciclagem, desempenhará um papel crucial na redução do impacto ambiental das operações de máquinas de perfuração.
Resumindo
Em resumo, selecionar a máquina de perfuração correta envolve consideração cuidadosa da especificidade da aplicação, especificações da máquina, tolerância e precisão, compatibilidade de material e custo. Avanços na tecnologia, como integração CNC, materiais de ferramentas avançadas e automação, estão impulsionando melhorias em eficiência, precisão e sustentabilidade. Considerações ambientais, incluindo eficiência energética, redução de resíduos e controle de emissões, estão se tornando cada vez mais importantes nas operações modernas de máquinas de perfuração. Tendências futuras, como manufatura inteligente, integração de manufatura aditiva e sustentabilidade, continuarão a moldar a indústria, oferecendo novas possibilidades e desafios para os fabricantes.