Spojrzenie na aktualne trendy i problemy z łańcuchem dostaw w sektorze motoryzacyjnym
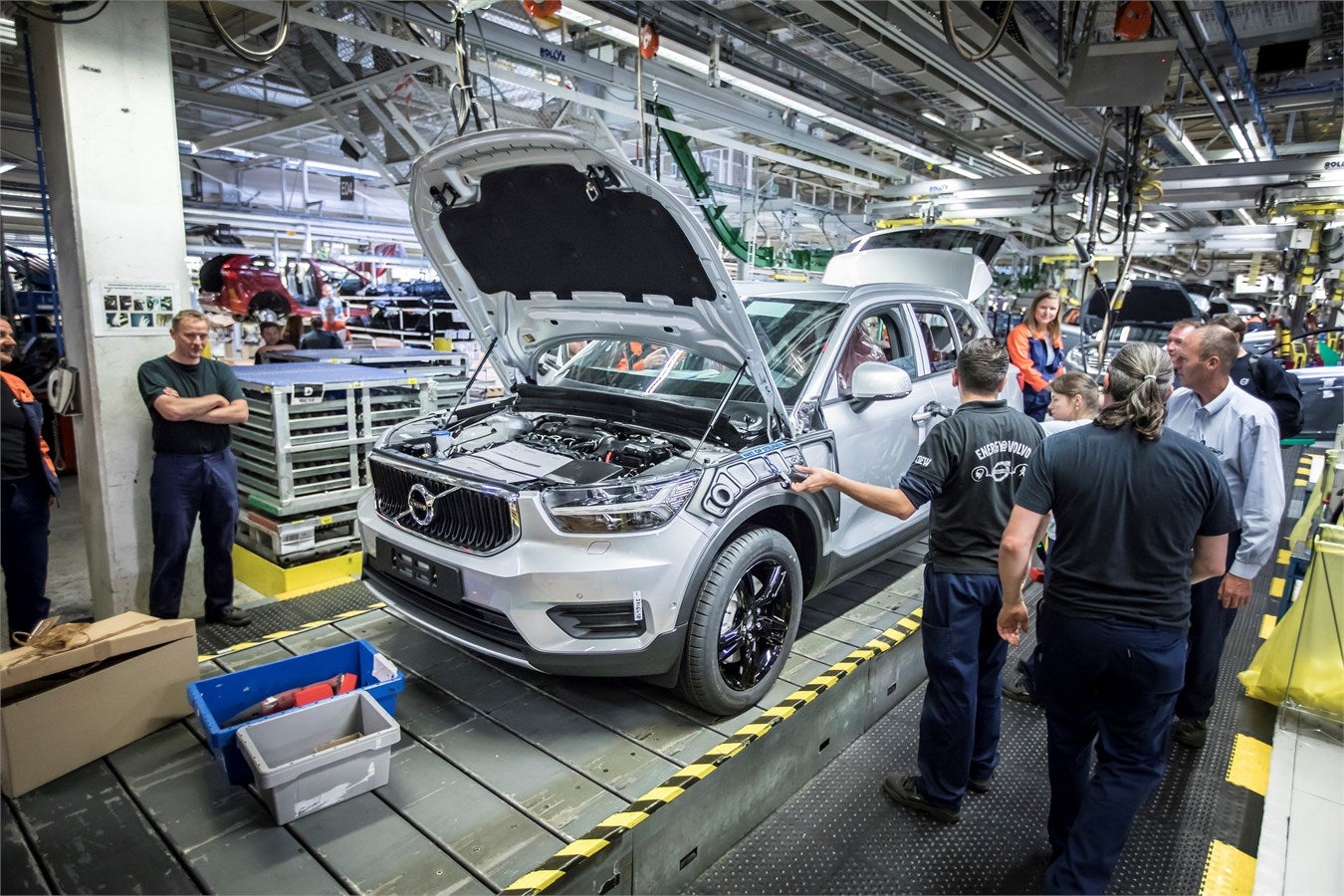
Nietypowy pojazd silnikowy może zawierać od 15,000 25,000 do XNUMX XNUMX części składowych – w zależności od sposobu ich pomiaru i inżynierii projektowej jego głównych systemów. To dużo materiału do zebrania i zapewnienia integralności produktu końcowego. Rzeczywiście, nie lada wyczynem jest złożenie wszystkich tych części we właściwej kolejności. Każdy istniejący samochód jest hołdem dla planowania procesów, organizacji, inżynierii produkcji i logistyki wytwarzania. Kiedyś producenci pojazdów byli wysoce zintegrowani pionowo, ale podejście to ustąpiło miejsca pozbawionym (ktoś pamięta, skąd wziął się Visteon i splątaną sieć firm, które obejmowały Automotive Components Group General Motors?) i specjalistycznym dostawcom części, którzy mogli skupić się na rozwoju produktu i działać wydajniej na większą skalę dla więcej niż jednego klienta.
Duzi integratorzy systemów pierwszego poziomu dostarczają swoje produkty bezpośrednio producentom pojazdów, często z parków dostawców dogodnie zlokalizowanych w pobliżu zakładów montażowych i produkcyjnych pojazdów, ale istnieje wiele mniejszych dostawców poniżej najwyższego poziomu – każdy z nich pełni istotną rolę na długiej drodze od surowców do gotowego produktu.
Międzynarodowe pozyskiwanie części składowych stało się standardowym sposobem działania branży przez wiele dziesięcioleci, ponieważ producenci OEM i więksi dostawcy starali się rozejrzeć na globalnym rynku za częściami i materiałami wejściowymi, które spełniają wymagane progi jakościowe przy najniższych kosztach. Odległości (i koszty) transportu i ustalenia dotyczące magazynowania również są częścią obrazu, ale wyższa wydajność i postęp technologiczny w międzynarodowej wysyłce towarowej poparły fenomenalny wzrost w międzynarodowych przesyłkach części.
Rozwój chińskiego przemysłu samochodowego w ciągu ostatnich dwóch dekad był również ważnym czynnikiem w globalnym pozyskiwaniu komponentów samochodowych, zwłaszcza tego, co można by nazwać uniwersalnymi lub komodowymi częściami, które sprzedają się głównie po cenie kosztowej. Chińscy dostawcy skorzystali na dużych lokalnych kontraktach, które zwiększają ekonomię skali, a także na ukrytych dotacjach płynących ze złożonych struktur własnościowych obejmujących spółki dominujące OEM, przedsiębiorstwa państwowe i zróżnicowane zapasy. Na początku XXI wieku amerykańscy producenci pojazdów, w szczególności, zaczęli pozyskiwać więcej tanich części z Azji, podkopując w ten sposób niektóre długo istniejące firmy w amerykańskiej bazie dostawców.
Na całym świecie międzynarodowe przepływy handlowe w produktach motoryzacyjnych – zarówno gotowych pojazdach, jak i częściach składowych – są obecnie ogromne. Szacunki zebrane przez GlobalData pokazują, że Niemcy są zdecydowanie światowym liderem międzynarodowym pod względem wysyłek wychodzących produktów przemysłu motoryzacyjnego. Eksport ten jest odzwierciedlony przez import i splątaną sieć dóbr pośrednich, które są wykorzystywane jako wkłady do systemów komponentów, które są udoskonalane i projektowane na różnych etapach procesu produkcyjnego i mogą być wysyłane przez granice międzynarodowe wielokrotnie.
Kolejną ważną cechą strukturalną łańcuchów dostaw w branży motoryzacyjnej jest znaczenie filozofii zarządzania łańcuchem dostaw, która minimalizuje koszty zapasów i zwiększa wydajność procesów oraz pętle komunikacji zwrotnej w celu poprawy standardów jakości. Znana jako „lean manufacturing”, zaczęła się od Toyoty, a jej istotę ujmuje termin „just-in-time”, aby opisać metody i zasady lean supply. Rozwój cyfrowych i połączonych technologii, które łączą wszystkie części procesu produkcji i sprzedaży detalicznej, dodatkowo wzmocnił te sposoby pracy w ciągu ostatniej dekady.
W przeszłości klęski żywiołowe i ich skoncentrowane skutki w różnych lokalizacjach miały wpływ na firmy motoryzacyjne i pokazały kruchość łańcuchów dostaw w branży motoryzacyjnej. Po trzęsieniu ziemi i tsunami w Japonii w 2011 r. pojawiło się kilka godnych uwagi przykładów zakłóceń. Globalny producent samochodów klasy premium miał problemy z dostawami lub dostawą czerwonego pigmentu do farb pochodzących z jednego źródła w Japonii. Powodzie w Tajlandii w tym samym roku spowodowały niedobór dostaw ekranów LCD do wyświetlaczy informacji o pojazdach. Producenci OEM i dealerzy musieli odpowiednio dostosować się do niedoborów. Wojna na Ukrainie pokazuje, jak nieoczekiwane wydarzenia geopolityczne mogą również zakłócić łańcuchy dostaw.
Wyzwanie półprzewodników
Wszystkie firmy zostały bezpośrednio negatywnie dotknięte kryzysem zdrowia publicznego w 2020 r., a pośrednio wieloma innymi skutkami dla globalnych łańcuchów dostaw. Ponadto odbudowa globalnej sprzedaży w 2021 r. została poważnie osłabiona przez nieprzewidziane konsekwencje kryzysu Covid rok wcześniej. Ponieważ producenci pojazdów zamknęli fabryki na mocy zarządzeń rządowych i drastycznie ograniczyli zamówienia na części w 2020 r., producenci półprzewodników znaleźli alternatywny biznes w takich obszarach jak elektronika użytkowa.
Kiedy w pierwszym kwartale 2021 r. odradzające się zakłady motoryzacyjne zwiększyły zamówienia na chipy, szybko ujawnił się problem ograniczonej podaży.
Niedobory półprzewodników również nie były łatwe do pokonania ze względu na długie terminy realizacji w celu dodania mocy produkcyjnych odlewni chipów w górnym biegu rzeki. Brak części, która jest krytyczna dla bezpieczeństwa lub w inny sposób uznana za niezbędną dla gotowego produktu, oznaczał, że niektóre linie modeli były dotknięte bardziej dotkliwie niż inne. Producenci pojazdów mogli w niektórych przypadkach przetasować miks rynkowy, ale stare przysłowie znów się sprawdzało: łańcuchy dostaw są tak dobre/solidne, jak ich najsłabszy punkt.
W całej branży metody i procesy zaopatrzenia są poddawane kontroli jak nigdy dotąd.
Warto również zauważyć, że istnieje element strukturalny, który oznacza, że niektóre naciski na dostawy półprzewodników prawdopodobnie pozostaną ryzykiem w przyszłości: zaawansowana zawartość elektroniki w pojazdach rośnie ze względu na stale rosnącą liczbę montowanych bardziej zaawansowanych technologicznie funkcji. To sprawia, że niektóre firmy przechodzą do strategicznych sojuszy z producentami chipów. Może to nie tylko pomóc w zabezpieczeniu przyszłych dostaw kluczowych mikroprocesorów, ale może również ułatwić korzystne relacje współpracy w zakresie przyszłego rozwoju produktu w tym, co staje się oczywiste, że jest strategicznie wartościowym obszarem komponentów.
Inne źródła presji na łańcuchy dostaw to m.in. nieprzewidziane niedobory siły roboczej i znacznie wyższe ceny międzynarodowych przesyłek kontenerowych spowodowane gwałtownym wzrostem cen energii.
Debata na temat podwójnego i wielokrotnego źródła
Kruchość w łańcuchach dostaw w branży motoryzacyjnej wiąże się z powszechnością wielu poziomów, przepływów międzynarodowych źródeł zaopatrzenia i tendencją do pojedynczego źródła zaopatrzenia w celu maksymalizacji oszczędności skali w ramach globalnych programów pojazdów. W wielu przypadkach ta tradycyjna struktura jest również osadzona i zakorzeniona w kulturze preferowanych partnerów na wszystkich poziomach dostaw. Zalety mogą również obejmować współdzielone systemy i koszty logistyczne, przy czym koszty rozkładają się na wolumeny w innych modelach i systemach.
Technologia również odegrała rolę w zachęcaniu do korzystania z jednego źródła, ponieważ firmy – w tym te z poziomów 3 i 4 – zazwyczaj były w stanie scentralizować wiedzę specjalistyczną i inwestycje w jednym zakładzie przeznaczonym do produkcji wielkoseryjnej. Problemy pojawiają się, gdy coś pójdzie nie tak i pokrzyżuje plany (na przykład pożar w fabryce mikroprocesorów Renesas w zeszłym roku).
Elektronika i czujniki to przykłady krytycznych komponentów podzespołów, które mogą mieć duże implikacje w dół łańcucha produkcji pojazdów, jeśli nastąpią jakiekolwiek zakłócenia w górę łańcucha. Znalezienie alternatywnych dostawców z wolnymi mocami produkcyjnymi w bardzo krótkim czasie jest dużym wyzwaniem.
Posiadanie pewnych rezerw części w zapasach wiąże się z kosztami i jest sprzeczne z zasadami szczupłej produkcji. Oczywiście można podjąć decyzję o pochłonięciu lub odpisaniu wszelkich kosztów zakłóceń odstających od normy w miarę ich występowania – ostatecznie zależy to od kwantyfikacji oceny ryzyka.
Doświadczenia ostatnich lat wskazują, że firmy coraz częściej zadają sobie pytanie, czy singe-sourcing jest tak pożądany, jak kiedyś. Świat naznaczony wyższym ryzykiem i niepewnością być może wymaga zmiany podejścia. Duplikacja w łańcuchu dostaw, nawet jeśli oznacza zbliżenie się do dzielenia się z konkurentem, może oferować lepsze rozwiązanie – przynajmniej w przypadku niektórych komponentów – niż single-sourcing. Korzyścią z dual-sourcingu byłoby większe bezpieczeństwo produktu. Jak zwykle, chodzi o ogólny koszt.
Elektryfikacja i nowe wzorce łańcucha dostaw
Elektryfikacja stawia nowe wyzwania przyszłym łańcuchom dostaw w motoryzacji. Producenci OEM stanęli w obliczu znacznych niepewności co do dostaw nowych i kluczowych komponentów – przede wszystkim akumulatorów układu napędowego – które próbują rozwiązać. Istnieją również strategiczne pytania dotyczące stopnia integracji pionowej, który jest pożądany w celu złagodzenia przyszłych ryzyk i sprawowania kontroli nad aspektami komercyjnymi ustaleń dotyczących dostaw. Utworzono joint ventures ze specjalistami od akumulatorów. Inne kluczowe komponenty pojazdów elektrycznych – takie jak silniki, części układu napędowego, falowniki wysokiego napięcia – będą również przedmiotem rosnących inwestycji wraz z rozważaniami dotyczącymi łańcucha dostaw.
Ambitne strategie elektryfikacji spowodują gwałtowny wzrost popytu na ogniwa baterii litowo-jonowych. Producenci baterii na całym świecie zobowiązują się do wielomiliardowych strategii ekspansji, otwierając nowe „gigafabryki”, aby dostarczać ogniwa producentom samochodów.
Jednym z godnych uwagi przykładów głębokiej współpracy OEM-Tier 1 w tej dziedzinie jest podpisanie MoU między Volkswagenem a Boschem. Obie firmy planują dostarczać zintegrowane systemy produkcji baterii, rozruch na miejscu i wsparcie konserwacyjne dla producentów ogniw i systemów baterii. Twierdzą, że dążą do uzyskania pozycji lidera pod względem kosztów i technologii w technologii baterii na skalę przemysłową oraz masowej produkcji „zrównoważonych, najnowocześniejszych baterii”.
Tylko w Europie Grupa Volkswagen planuje zbudować sześć fabryk ogniw do 2030 r., a inni producenci podejmują podobne kroki, aby zabezpieczyć przyszłe dostawy ogniw i akumulatorów. Do 700 r. region powinien osiągnąć całkowitą roczną pojemność akumulatorów wynoszącą około 2030 gigawatogodzin.
Patrząc w górę rzeki, Toyota utworzyła spółkę joint venture z Panasonic (Prime Planet Energy & Solutions – PPES), która podpisała umowę z gigantem górniczym BHP na przyszłe dostawy siarczanu niklu, podstawy niklu obecnego w katodzie większości ogniw baterii litowo-jonowych. Tesla również podpisała podobną umowę z BHP, co pokazuje, że surowce są również bardzo istotne dla przyszłego bezpieczeństwa dostaw.
Transakcje te podkreślają potrzebę, aby gracze motoryzacyjni przyjrzeli się bliżej łańcuchowi dostaw baterii, aby mieć pewność, że mają dostęp do wystarczającej ilości surowców, aby zapewnić ogromny wzrost mocy produkcyjnych potrzebny w sektorze baterii litowo-jonowych dla nowej fali pojazdów elektrycznych zasilanych bateriami, która pojawi się w nadchodzących latach. Recykling jest również kluczowym czynnikiem w wielu zawartych transakcjach.
Blockchain dla przejrzystości łańcucha dostaw
Firmy motoryzacyjne coraz częściej wykorzystują technologię blockchain, aby uzyskać przejrzystość w kwestiach łańcucha dostaw, takich jak emisja CO2 i źródło kobaltu do akumulatorów (co może wiązać się z pytaniami etycznymi dotyczącymi wydobycia cennych minerałów).
Pierwotna koncepcja blockchain, jak sama nazwa wskazuje, to łańcuch bloków lub rekordów oznaczonych znacznikiem czasu (blok = informacje cyfrowe; łańcuch = baza danych publiczna/społecznościowa). Bloki przechowują informacje o transakcjach. Kiedy blok przechowuje nowe dane – transakcję – jest ona dodawana do blockchain i po zweryfikowaniu przez sieć peer-to-peer komputerów, każdy może ją zobaczyć (lub może podlegać zezwoleniu prywatnej sieci, takiej jak łańcuch dostaw OEM – „rozproszony rejestr”).
Jednak wszystkie strony mają dostęp tylko do informacji, do których mają uprawnienia. Każdy komputer w sieci blockchain ma swoją własną kopię blockchain. Zasadniczo jednak chodzi o stworzenie wysoce przejrzystego systemu z zerowymi kosztami transakcji między dwiema stronami tworzącymi blok.
Możemy się spodziewać, że więcej firm motoryzacyjnych zacznie stosować procesy oparte na technologii blockchain – zwłaszcza te oparte na rozproszonym rejestrze (czyli sieci prywatnej) – jako sposób na ograniczenie ryzyka „przerwania” łańcucha dostaw i zrozumienie mocnych i słabych stron wzdłuż łańcucha, ale także jako sposób na zademonstrowanie rosnących wymagań dotyczących zgodności w obszarach regulacyjnych, takich jak zrównoważony rozwój.
Lekcje z Toyoty
Toyota jest powszechnie postrzegana jako jedna z najlepszych firm w branży motoryzacyjnej, jeśli chodzi o zarządzanie łańcuchem dostaw. Oprócz tego, że jest twórcą metod produkcji szczupłej, które później stały się powszechną najlepszą praktyką przyjętą przez większość producentów OEM i głównych dostawców, udoskonaliła również swoje systemy i procesy zgodnie ze zmieniającymi się okolicznościami dotyczącymi środków łagodzenia ryzyka. Ponadto, współpracowała bardzo ściśle ze swoimi dostawcami w czasie i w interesie szerszych celów sektora w obliczu sytuacji awaryjnych.
Po trzęsieniu ziemi i tsunami w Kioto w 2011 r. Toyota współpracowała z dostawcami w Japonii, aby stworzyć kompleksową bazę danych informacji o łańcuchu dostaw, aby wesprzeć japoński sektor produkcyjny. Toyota wprowadziła również strategię wielokrotnego pozyskiwania kluczowych części, co oznaczałoby zorganizowanie dostaw z trzech różnych źródeł – ale główny dostawca byłby nastawiony na realizację prawie dwóch trzecich zamówienia, aby zapewnić ekonomię skali. Wielu dostawców rzeczywiście osłabia ekonomię skali, ale oznacza to również, że w razie potrzeby istnieją alternatywy.
Toyota ma również dobrze rozwinięty system monitorowania swojej rozległej sieci dostawców i system wczesnego ostrzegania o niedoborach. Rzeczywiście, niektóre firmy zwracają się do AI, aby ocenić rozwój swoich łańcuchów dostaw – chociaż opiera się to na posiadaniu niezawodnej, rozległej i szczegółowej bazy danych.
Inną opcją dla firm jest utrzymywanie zapasów awaryjnych lub buforowych kluczowych części – szczególnie tych, które mogą spowodować zatrzymanie linii produkcyjnej. Ponownie, wiąże się to z dodatkowymi kosztami magazynowania lub składowania, ale jest to kwestia podjęcia decyzji, jaki poziom kosztów lub „składki ubezpieczeniowej” jest warty zapłaty. Ponadto nie będzie to rozwiązanie trwałe. Toyota mogła zgromadzić zapasy niektórych półprzewodników, ale skala globalnego niedoboru chipów oznaczała, że ostatecznie również ona została zmuszona do ograniczenia produkcji. Być może najważniejszą nauką, jaką wyniosła Toyota, jest potrzeba ciągłego przeglądu i dostosowywania się do zmieniających się okoliczności i niepewności.
Źródło z Po prostu Auto
Zastrzeżenie: Informacje podane powyżej są dostarczane przez just-auto.com niezależnie od Cooig.com. Cooig.com nie składa żadnych oświadczeń ani gwarancji co do jakości i niezawodności sprzedawcy i produktów.