W 2025 r. globalny rynek maszyn EDM jest wyceniany na 4.5 mld USD, napędzany postępem technologicznym i rosnącym popytem na precyzyjną obróbkę. Niniejszy artykuł zawiera dogłębną analizę kluczowych czynników przy wyborze maszyn EDM, w tym wydajności, typów i kwestii kosztów, dostarczając cennych spostrzeżeń i pomocy dla profesjonalnych nabywców w różnych branżach. Przechodząc od przeglądu rynku do praktycznych zastosowań, ten przewodnik zapewnia świadome podejmowanie decyzji.
Spis treści:
– Przegląd rynku maszyn EDM
– Szczegółowe wprowadzenie i analiza rynku maszyn EDM
– Kluczowe czynniki przy wyborze maszyny EDM
– Rozważania nad kosztami i budżetem
– Praktyczne zastosowania maszyn EDM
– Konserwacja i utrzymanie maszyn EDM
- Końcowe przemyślenia
Przegląd rynku maszyn EDM
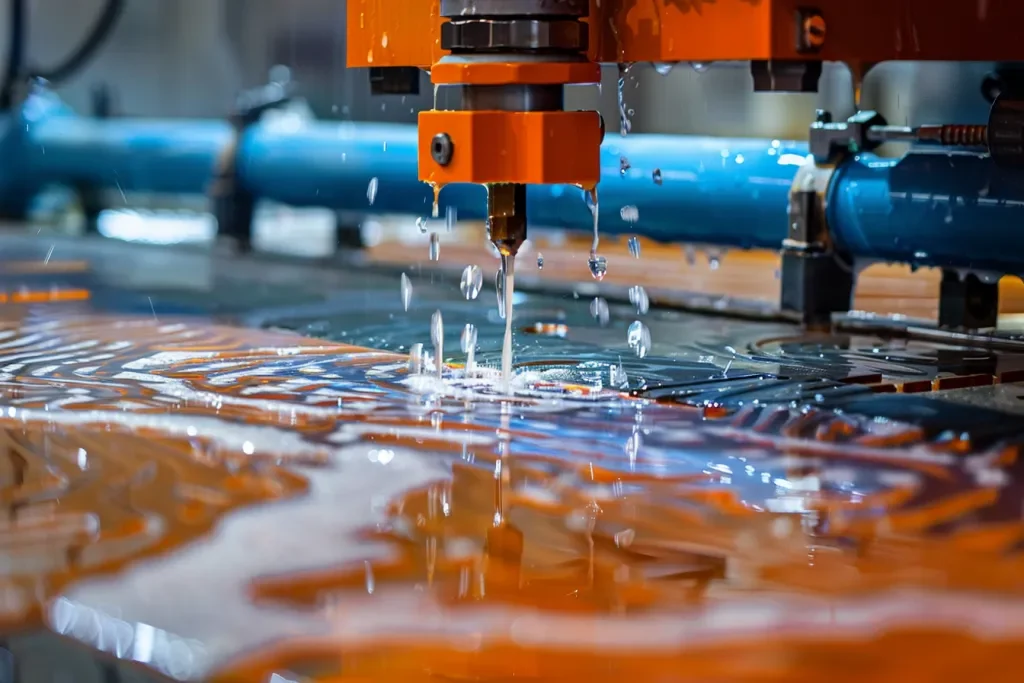
Globalny rynek obróbki elektroerozyjnej (EDM) doświadcza znacznego wzrostu ze względu na postęp w technologiach produkcyjnych i rosnący popyt ze strony różnych branż. Do 2025 r. rynek EDM jest wyceniany na około 4.5 mld USD, przy prognozowanym rocznym tempie wzrostu (CAGR) wynoszącym 6.1% do 2030 r. Wzrost ten jest napędzany rosnącym zapotrzebowaniem na precyzyjną obróbkę w sektorach takich jak motoryzacja, lotnictwo i opieka zdrowotna.
Ameryka Północna i Europa łącznie odpowiadają za ponad 60% globalnego udziału w rynku EDM, przy czym Stany Zjednoczone i Niemcy są kluczowymi uczestnikami ze względu na ich silne bazy przemysłowe i postęp technologiczny. Tymczasem region Azji i Pacyfiku doświadcza szybkiego wzrostu, szczególnie w Chinach, Japonii i Indiach, napędzanego zwiększoną industrializacją i inwestycjami w zaawansowane technologie produkcyjne. Oczekuje się, że region będzie rósł w tempie CAGR wynoszącym 7.3% w okresie prognozowania.
Rynek jest podzielony na różne typy maszyn EDM, w tym Die Sinking EDM, Wire EDM i Hole Drilling EDM. Wire EDM ma największy udział w rynku, stanowiąc 45% całkowitego rynku, ze względu na jego szerokie zastosowanie w produkcji złożonych i precyzyjnych komponentów. Sektor motoryzacyjny pozostaje największą branżą użytkowników końcowych, stanowiąc 35% całkowitego popytu rynkowego, tuż za nim znajdują się sektory lotnictwa i opieki zdrowotnej.
Szczegółowe wprowadzenie i analiza rynku maszyn EDM
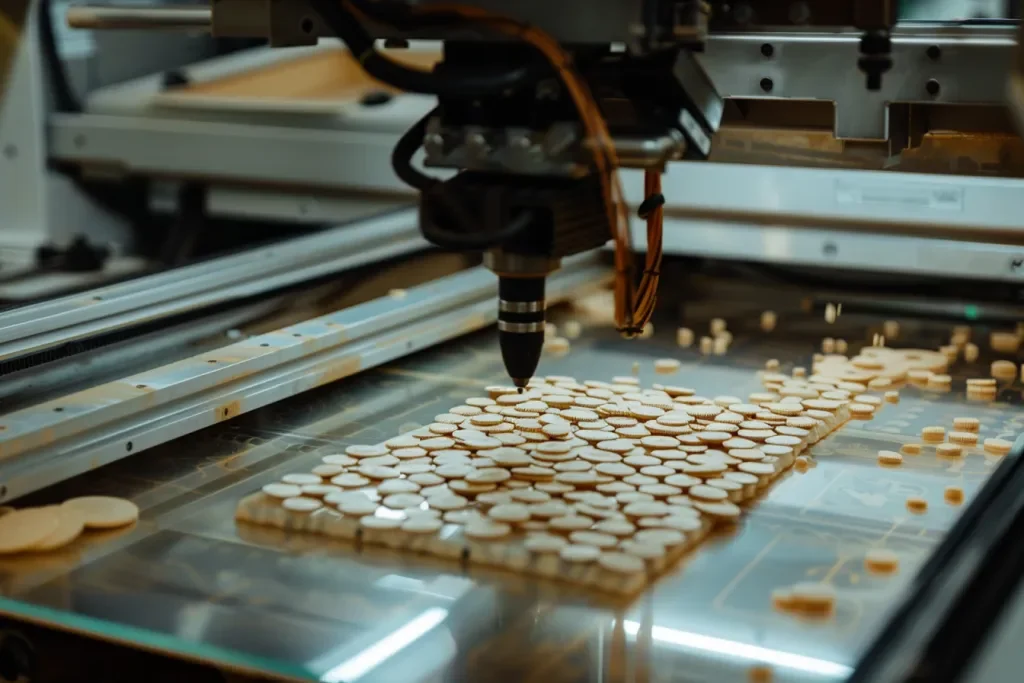
Maszyny EDM są niezbędne w branżach wymagających wysokiej precyzji i złożonych geometrii, których nie można osiągnąć tradycyjnymi metodami obróbki. Kluczowe parametry wydajności maszyn EDM obejmują wysoką dokładność, jakość wykończenia powierzchni i szybkość usuwania materiału. Nowoczesne maszyny EDM oferują precyzję rzędu mikronów, co czyni je niezbędnymi do produkcji krytycznych komponentów w przemyśle lotniczym i urządzeniach medycznych.
Dynamika rynku jest w dużym stopniu uzależniona od przyjęcia zaawansowanych technologii, takich jak komputerowe sterowanie numeryczne (CNC) i automatyzacja. Maszyny CNC EDM, które stanowią 70% rynku, zapewniają doskonałą dokładność i powtarzalność, co napędza ich powszechne przyjęcie. Ponadto innowacje, takie jak adaptacyjne systemy sterowania i monitorowanie w czasie rzeczywistym, zwiększają wydajność i efektywność maszyn EDM, redukując przestoje i koszty operacyjne.
Czynniki ekonomiczne, takie jak rosnące koszty surowców i siły roboczej, skłaniają producentów do inwestowania w technologię EDM w celu zwiększenia wydajności i ograniczenia odpadów. Ponadto zachowania konsumentów zmieniają się w kierunku wysokiej jakości, trwałych produktów, zwiększając popyt na precyzyjne rozwiązania obróbcze. Kanały dystrybucji maszyn EDM są głównie za pośrednictwem dealerów i dystrybutorów, którzy mają 55% udział w rynku ze względu na swoje rozległe sieci i możliwości wsparcia posprzedażowego.
Ostatnie innowacje na rynku EDM obejmują integrację Internetu rzeczy (IoT) i sztucznej inteligencji (AI) w celu predykcyjnej konserwacji i optymalizacji procesów. Na przykład maszyny EDM z obsługą IoT mogą monitorować dane w czasie rzeczywistym, aby przewidywać awarie sprzętu i planować konserwację, zmniejszając nieplanowane przestoje nawet o 20%. Algorytmy AI są również wykorzystywane do optymalizacji parametrów obróbki, poprawiając szybkość usuwania materiału i wykończenie powierzchni.
Cykl życia produktu maszyn EDM trwa zazwyczaj 10-15 lat, a regularne uaktualnienia i konserwacja są wymagane do utrzymania optymalnej wydajności. Trend digitalizacji napędza adopcję inteligentnych rozwiązań EDM, które oferują ulepszoną łączność i możliwości analizy danych, zapewniając producentom cenne informacje na temat procesów obróbki.
Kluczowe czynniki przy wyborze maszyny EDM
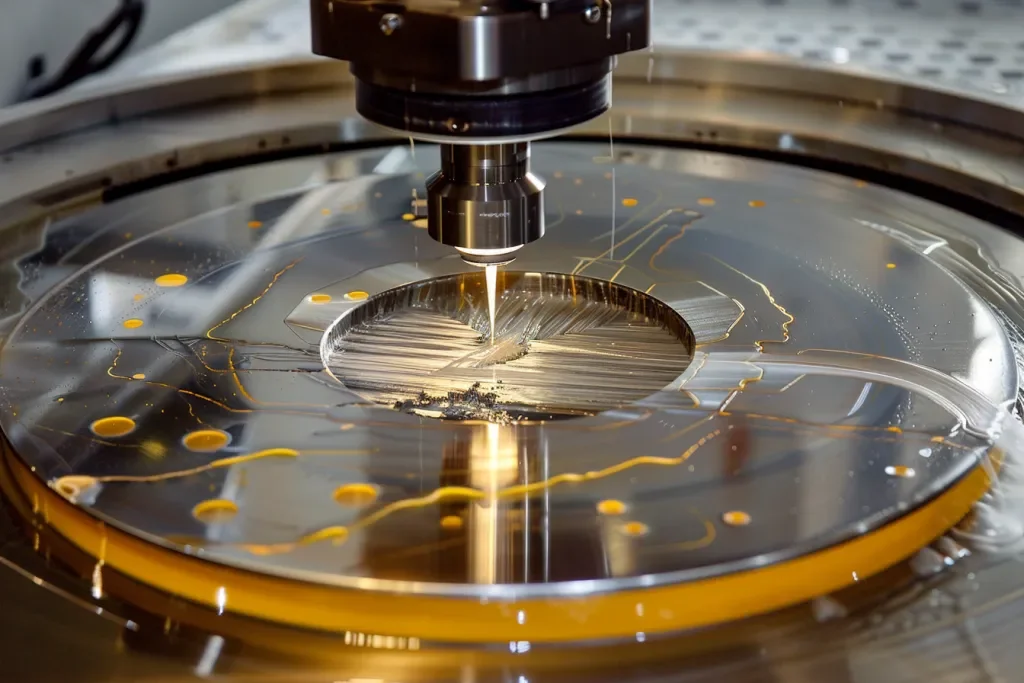
Wybór właściwej maszyny do obróbki elektroerozyjnej (EDM) jest kluczowy dla osiągnięcia precyzji i wydajności w procesach produkcyjnych. Należy wziąć pod uwagę kilka czynników, aby mieć pewność, że wybrana maszyna spełnia konkretne potrzeby Twoich zastosowań.
Wydajność i funkcjonalność
Wydajność i funkcjonalność są najważniejsze przy wyborze maszyny EDM. Maszyny te wykorzystują wyładowania elektryczne do erozji materiału, dzięki czemu nadają się do twardych metali i skomplikowanych kształtów. Kluczowe wskaźniki wydajności obejmują prędkość cięcia, dokładność i jakość wykończenia powierzchni. Prędkość cięcia zależy od zasilania i rodzaju użytego płynu dielektrycznego. Szybkie maszyny EDM mogą znacznie skrócić czas produkcji, co jest korzystne w przypadku produkcji wielkoseryjnej. Dokładność, często mierzona w mikronach, jest kolejnym krytycznym aspektem. Maszyny z zaawansowanymi systemami sterowania i mechanizmami sprzężenia zwrotnego mogą oferować precyzyjne cięcia, niezbędne w takich branżach jak przemysł lotniczy i produkcja urządzeń medycznych. Jakość wykończenia powierzchni jest określana przez materiał elektrody i ustawienia energii wyładowania. Maszyny, które umożliwiają precyzyjne dostrajanie tych parametrów, mogą wytwarzać gładsze wykończenia, zmniejszając potrzebę obróbki końcowej. Zaawansowane maszyny EDM często są wyposażone w adaptacyjne systemy sterowania, które automatycznie dostosowują ustawienia w celu utrzymania optymalnej wydajności.
Rodzaje maszyn EDM
Zrozumienie różnych typów maszyn EDM jest niezbędne, aby dopasować maszynę do swoich konkretnych wymagań. Dwa główne typy to EDM wgłębne i EDM wycinane drutem, każdy z odrębnymi zastosowaniami i korzyściami. EDM wgłębne, znane również jako EDM Ram, wykorzystuje ukształtowaną elektrodę do tworzenia wnęk w obrabianym przedmiocie. Ten typ jest idealny do tworzenia złożonych form i matryc, szczególnie w przemyśle motoryzacyjnym i elektronicznym. Maszyny EDM wgłębne są znane ze swojej zdolności do obsługi skomplikowanych geometrii i głębokich wnęk z dużą precyzją. EDM wycinane drutem wykorzystuje cienki drut jako elektrodę do przecinania obrabianego przedmiotu. Jest wysoce skuteczny w obróbce złożonych kształtów i konturów, dzięki czemu nadaje się do takich branż jak przemysł lotniczy i produkcja narzędzi. Maszyny EDM wycinane drutem oferują wysoką dokładność i mogą wytwarzać części o drobnych szczegółach i ścisłych tolerancjach. Ponadto istnieją specjalistyczne maszyny EDM, takie jak EDM do małych otworów do wiercenia drobnych otworów i maszyny CNC EDM, które oferują zautomatyzowane i programowalne operacje do produkcji wielkoseryjnej.
Najnowsze funkcje technologiczne
Krajobraz technologii EDM nieustannie ewoluuje, a nowe funkcje zwiększają możliwości maszyn i komfort użytkowania. Nowoczesne maszyny EDM są wyposażone w zaawansowane systemy sterowania, automatyzację i opcje łączności. Systemy sterowania z interfejsami z ekranem dotykowym i intuicyjnym oprogramowaniem ułatwiają konfigurację i obsługę maszyny. Systemy te często obejmują wstępnie zaprogramowane cykle obróbki i monitorowanie w czasie rzeczywistym, co pozwala operatorom optymalizować proces i skracać przestoje. Funkcje automatyzacji, takie jak ramiona robotyczne i automatyczne zmieniacze narzędzi, mogą dodatkowo zwiększyć produktywność, umożliwiając ciągłą pracę przy minimalnej ingerencji człowieka. Funkcje te są szczególnie korzystne w środowiskach produkcji wielkoseryjnej, w których wydajność i spójność mają kluczowe znaczenie. Opcje łączności, w tym integracja IoT i zdalne monitorowanie, umożliwiają lepsze zarządzanie maszyną i jej konserwację. Operatorzy mogą uzyskiwać dostęp do danych maszyny i diagnostyki w czasie rzeczywistym, co umożliwia konserwację predykcyjną i skraca nieoczekiwane przestoje.
Jakość wykonania i trwałość
Jakość wykonania i trwałość maszyny EDM to kluczowe czynniki wpływające na jej wydajność i żywotność. Maszyny zbudowane z wysokiej jakości materiałów i solidnych komponentów są w stanie wytrzymać trudy ciągłej pracy i zachować dokładność w czasie. Rama maszyny i elementy konstrukcyjne powinny być wykonane ze sztywnych materiałów, takich jak żeliwo lub granit, aby zminimalizować drgania i zapewnić stabilność. Wysokoprecyzyjne prowadnice liniowe i śruby kulowe są również niezbędne do utrzymania dokładności i płynnego ruchu. Trwałość jest dodatkowo zwiększana przez takie cechy, jak uszczelnione obudowy i osłony ochronne, które chronią krytyczne elementy przed kurzem i zanieczyszczeniami. Regularna konserwacja i właściwe smarowanie ruchomych części są również kluczowe dla wydłużenia żywotności maszyny.
Efektywność energetyczna i wpływ na środowisko
Wydajność energetyczna jest coraz ważniejszym czynnikiem dla producentów, którzy chcą obniżyć koszty operacyjne i zminimalizować swój ślad środowiskowy. Nowoczesne maszyny EDM są projektowane tak, aby były bardziej energooszczędne, z takimi funkcjami jak tryby oszczędzania energii i wydajne zasilacze. Tryby oszczędzania energii zmniejszają zużycie energii w czasie bezczynności, podczas gdy wydajne zasilacze zapewniają optymalne wykorzystanie energii podczas operacji obróbki. Te funkcje nie tylko obniżają rachunki za prąd, ale również przyczyniają się do bardziej ekologicznego procesu produkcyjnego. Ponadto wybór płynów dielektrycznych może mieć wpływ na ślad środowiskowy. Dostępne są przyjazne dla środowiska płyny dielektryczne, które są biodegradowalne i nietoksyczne, co zmniejsza wpływ procesu EDM na środowisko.
Rozważania nad kosztami i budżetem
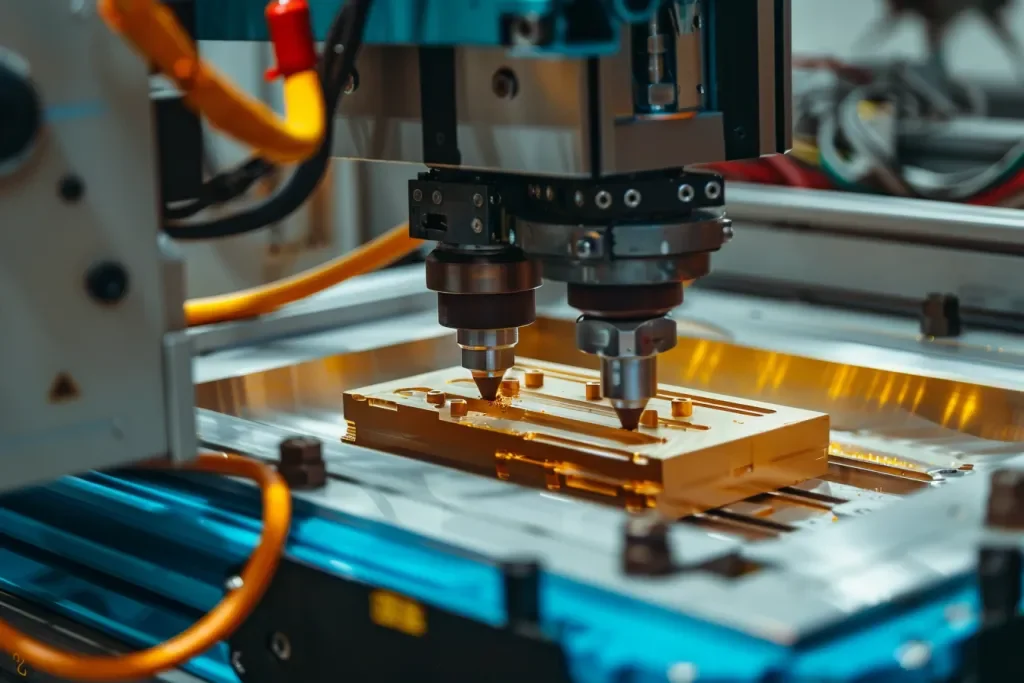
Wybierając maszynę EDM, istotne jest zrównoważenie początkowej inwestycji z długoterminowymi kosztami operacyjnymi i potencjalnym zwrotem z inwestycji. Cena maszyn EDM może się znacznie różnić w zależności od takich czynników, jak typ, rozmiar i funkcje. Koszty początkowe obejmują cenę zakupu, instalację oraz wszelkie niezbędne akcesoria lub narzędzia. Ważne jest, aby wziąć pod uwagę całkowity koszt posiadania, który obejmuje koszty konserwacji, materiałów eksploatacyjnych i energii. Maszyny o wyższych kosztach początkowych mogą oferować lepszą wydajność, trwałość i niższe koszty operacyjne, co z czasem prowadzi do wyższego zwrotu z inwestycji. Dostępne są również opcje finansowania i programy leasingowe, dzięki czemu producenci mogą nabywać zaawansowane maszyny EDM bez znacznej początkowej inwestycji. Zaleca się ocenę różnych opcji finansowania i wybranie tej, która najlepiej odpowiada Twojemu budżetowi i celom finansowym.
Praktyczne zastosowania maszyn EDM
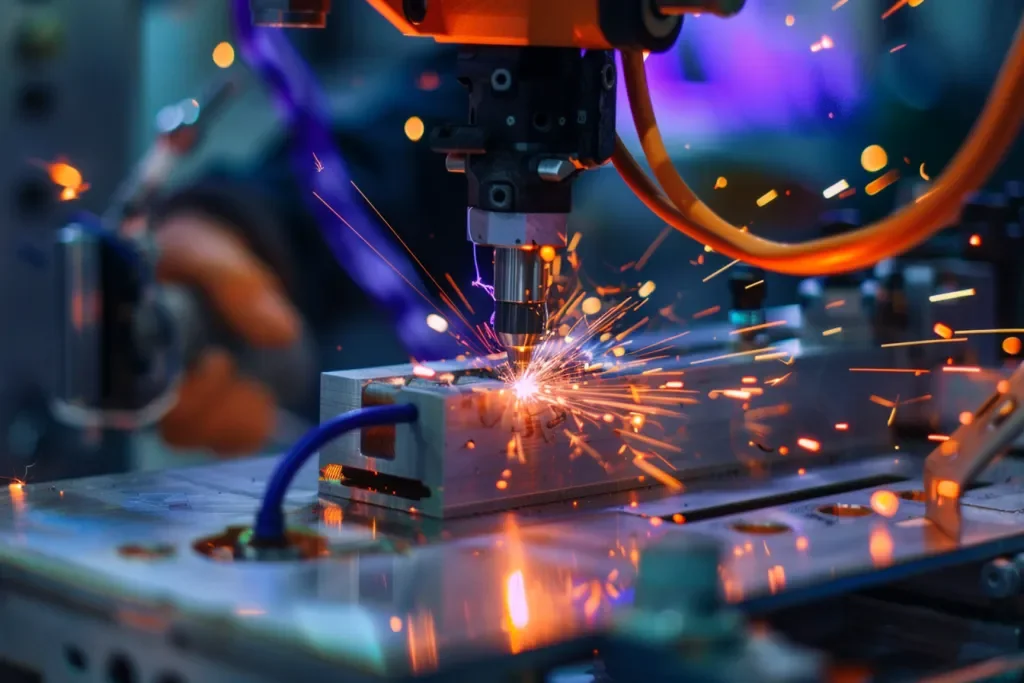
Maszyny EDM są wszechstronne i znajdują zastosowanie w różnych branżach, z których każda ma specyficzne wymagania i wyzwania. Zrozumienie tych zastosowań może pomóc w wyborze odpowiedniej maszyny do Twoich potrzeb.
Przemysł lotniczy
W przemyśle lotniczym maszyny EDM są używane do produkcji złożonych komponentów o wysokiej precyzji i ścisłych tolerancjach. Należą do nich łopatki turbin, komponenty silników i części konstrukcyjne. Możliwość obróbki twardych materiałów, takich jak tytan i Inconel, sprawia, że EDM jest idealnym wyborem do zastosowań lotniczych.
Produkcja urządzeń medycznych
Produkcja urządzeń medycznych wymaga wysokiej precyzji i doskonałego wykończenia powierzchni, aby spełnić surowe normy regulacyjne. Maszyny EDM są używane do produkcji narzędzi chirurgicznych, implantów i innych elementów medycznych. Możliwość obróbki małych, skomplikowanych części z dużą dokładnością jest kluczowa w tej branży.
Branża motoryzacyjna
Przemysł motoryzacyjny wykorzystuje maszyny EDM do produkcji form, matryc i precyzyjnych komponentów. Maszyny te są niezbędne do produkcji złożonych części o wysokiej powtarzalności i spójności. Możliwość obróbki różnych materiałów, w tym stali hartowanych, jest znaczącą zaletą w produkcji motoryzacyjnej.
Tworzenie narzędzi i matryc
Maszyny EDM są szeroko stosowane w przemyśle narzędziowym do tworzenia form, matryc i elementów narzędziowych. Precyzja i możliwość wytwarzania złożonych geometrii sprawiają, że EDM jest niezbędną technologią dla tej branży. Zastosowanie wysokiej jakości elektrod i zaawansowanych systemów sterowania zapewnia produkcję dokładnych i niezawodnych narzędzi.
Konserwacja i utrzymanie maszyn EDM
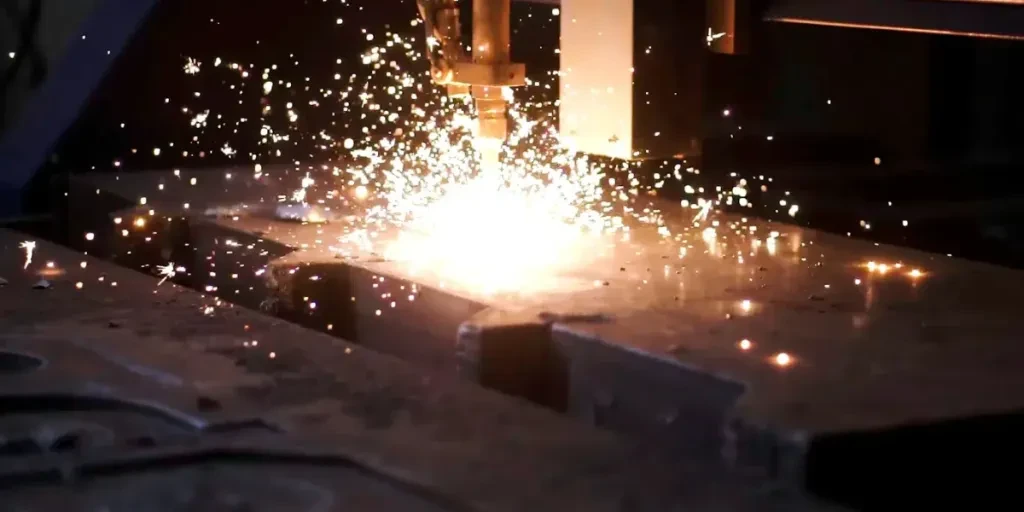
Regularna konserwacja i właściwe utrzymanie są niezbędne do zapewnienia optymalnej wydajności i długowieczności maszyn EDM. Dobrze utrzymana maszyna może zapewniać spójne wyniki i zmniejszać ryzyko nieoczekiwanych przestojów.
Rutynowa konserwacja
Rutynowe czynności konserwacyjne obejmują czyszczenie maszyny, sprawdzanie i wymianę materiałów eksploatacyjnych oraz smarowanie ruchomych części. Regularna kontrola krytycznych komponentów, takich jak elektrody, filtry i płyn dielektryczny, jest konieczna, aby zapewnić optymalną wydajność. Utrzymywanie maszyny w czystości i bez zanieczyszczeń może zapobiec problemom związanym z zanieczyszczeniem i zużyciem.
Konserwacja Zapobiegawcza
Konserwacja zapobiegawcza obejmuje zaplanowane inspekcje i serwisowanie w celu identyfikacji i rozwiązania potencjalnych problemów, zanim doprowadzą do awarii maszyny. Obejmuje to sprawdzanie połączeń elektrycznych, inspekcję podzespołów mechanicznych pod kątem zużycia i kalibrację maszyny w celu zachowania dokładności. Wdrożenie planu konserwacji zapobiegawczej może wydłużyć żywotność maszyny i poprawić ogólną niezawodność.
Modernizacja i modernizacja
Wraz z postępem technologii, modernizacja lub doposażenie istniejących maszyn EDM może zwiększyć ich możliwości i wydłużyć ich żywotność. Modernizacje mogą obejmować instalację zaawansowanych systemów sterowania, dodawanie funkcji automatyzacji lub włączanie energooszczędnych komponentów. Modernizacja może poprawić wydajność maszyny, obniżyć koszty operacyjne i zwiększyć produktywność.
Uwagi końcowe
Podsumowując, wybór odpowiedniej maszyny EDM wymaga starannego rozważenia różnych czynników, w tym wydajności, funkcjonalności, jakości wykonania i kosztów. Zrozumienie konkretnych wymagań Twojej aplikacji i ocena dostępnych opcji może pomóc Ci podjąć świadomą decyzję. Regularna konserwacja i potencjalne ulepszenia mogą dodatkowo zwiększyć wydajność i trwałość maszyny, zapewniając wysoki zwrot z inwestycji.