W Additive Manufacturing Campus w Oberschleißheim, BMW Group testuje produkcję addytywną łukiem drutowym (WAAM), w której drut wykonany z aluminium lub podobnego materiału jest topiony za pomocą łuku. Następnie robot sterowany przez oprogramowanie precyzyjnie umieszcza dużą liczbę spoin jedna na drugiej, aż do ukończenia kompletnego komponentu.
Ponieważ ciśnienie sprawia, że warstwa po warstwie nie trzeba zwracać uwagi na możliwość odformowania, możliwe jest tworzenie pustych struktur o optymalnym stosunku sztywności do masy.
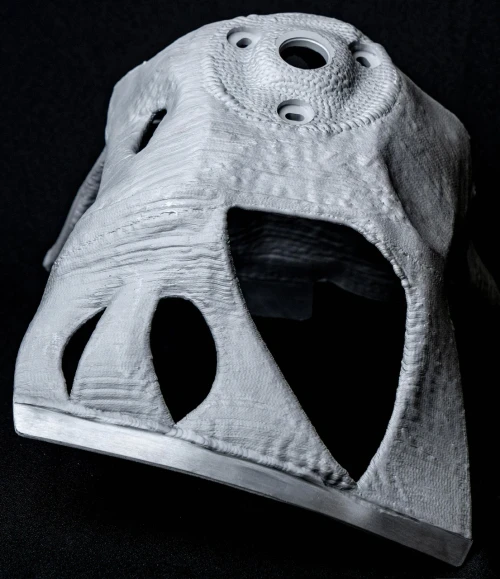
Oznacza to, że komponenty mogą być lżejsze i sztywniejsze niż porównywalne części odlewane ciśnieniowo obecnie produkowane seryjnie. Mogą być również produkowane w sposób bardziej zrównoważony dzięki niższym wymaganiom energetycznym i mniejszej ilości odpadów materiałowych. W przyszłości plan zakłada wykorzystanie komponentów wyprodukowanych w procesie WAAM w pojazdach produkcyjnych BMW Group.
Duża szerokość i wysokość pojedynczego szwu spawalniczego oznacza, że komponenty mogą być produkowane niezwykle szybko przy użyciu WAAM. W przeciwieństwie do topienia wiązką laserową, które jest już stosowane w prototypach i produkcji małoseryjnej w BMW Group, WAAM jest szczególnie odpowiednie dla większych komponentów. Typowe grubości ścianek są dobrze dostosowane do komponentów w obszarach nadwozia, napędu i podwozia. Jednak narzędzia i urządzenia mogą być również produkowane przy użyciu tego zaawansowanego technologicznie procesu, który jest również stosowany w przemyśle lotniczym.
Pracownicy BMW Group skupiają się na procesie WAAM, znanym również jako spawanie narastające, od 2015 roku. Komórka WAAM do produkcji komponentów testowych jest używana w Additive Manufacturing Campus od 2021 roku. Jednym z takich przykładowych zastosowań jest wspornik kolumny zawieszenia, który w obszernych testach na stanowisku testowym jest porównywany z komponentem produkowanym seryjnie, wykonanym z aluminiowego odlewu ciśnieniowego.
Na tym wczesnym etapie jest już jasne, że proces WAAM może skutkować niższymi emisjami w procesie produkcyjnym. Niższa waga komponentów, korzystny współczynnik wykorzystania materiałów i możliwość wykorzystania energii odnawialnej oznaczają, że komponenty mogą być produkowane wydajniej.
—Jens Ertel, szef działu produkcji addytywnej w BMW
Kolejnym etapem na drodze do produkcji seryjnej jest testowanie podzespołów pojazdu, które rozpocznie się w niedalekiej przyszłości.
Szersze spoiny w procesie WAAM oznaczają, że powierzchnie komponentów nie są gładkie, ale lekko pofalowane i muszą być wykończone w newralgicznych miejscach. Jednak inżynierowie BMW Group byli w stanie wykazać, że komponenty WAAM mogą być używane do dużych obciążeń, w tym obciążeń cyklicznych, nawet bez obróbki końcowej powierzchni.
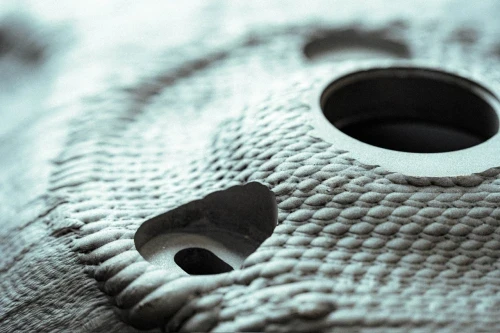
Zoptymalizowane parametry procesu mają kluczowe znaczenie dla zapewnienia trwałości już od samego początku produkcji, dlatego proces spawania i planowanie ścieżki robota muszą być optymalnie skoordynowane.
Aby optymalnie wykorzystać komponenty wytworzone w procesie WAAM, najważniejsze jest połączenie procesu produkcyjnego i ogólnego nowego projektu komponentu. W tym celu BMW Group nadal przyspiesza wykorzystanie projektowania generatywnego. W tym przypadku komputer wykorzystuje algorytmy do projektowania zoptymalizowanych komponentów w oparciu o konkretne wymagania.
Algorytmy te są opracowywane w ścisłej współpracy z interdyscyplinarnymi zespołami i są częściowo inspirowane procesami ewolucyjnymi w naturze. Podobnie jak w przypadku struktur bionicznych, pierwszym krokiem jest użycie tylko materiału, który jest faktycznie wymagany do topologii komponentu, a podczas dostrajania w drugim kroku komponent jest wzmacniany tylko tam, gdzie jest to konieczne. Ostatecznie skutkuje to lżejszymi i sztywniejszymi komponentami, a także większą wydajnością i ulepszoną dynamiką pojazdu.
Różne procesy produkcji addytywnej niekoniecznie ze sobą konkurują, raczej powinny być postrzegane jako uzupełniające się. Na przykład topienie wiązką laserową będzie nadal korzystniejsze niż proces WAAM, jeśli chodzi o najwyższy poziom rozdzielczości szczegółów. Jednak pod względem możliwego rozmiaru komponentu i szybkości osadzania, produkcja addytywna łukiem drutowym jest lepsza.
BMW Group początkowo planuje scentralizowaną produkcję WAAM komponentów w Oberschleißheim, w przyszłości możliwa jest również produkcja w innych lokalizacjach i wykorzystanie technologii przez dostawców. Ponadto możliwe byłoby nawet wytwarzanie poszczególnych komponentów bezpośrednio na linii montażowej przy użyciu tego procesu i wytwarzanie różnych części bez nowych narzędzi, po prostu poprzez zmianę oprogramowania. Zrównoważony rozwój można również dalej poprawić, zwiększając wykorzystanie metali pochodzących z recyklingu.
Źródło z Kongres Zielonych Samochodów
Zastrzeżenie: Informacje podane powyżej są dostarczane przez greencarcongress.com niezależnie od Cooig.com. Cooig.com nie składa żadnych oświadczeń ani gwarancji co do jakości i niezawodności sprzedawcy i produktów.