Op de Additive Manufacturing Campus in Oberschleißheim test de BMW Group Wire Arc Additive Manufacturing (WAAM), waarbij een draad van aluminium of iets dergelijks met een boog wordt gesmolten. Vervolgens plaatst een softwaregestuurde robot een groot aantal lasnaden nauwkeurig op elkaar, totdat een compleet onderdeel is voltooid.
Omdat door de druk laag voor laag geen aandacht hoeft te worden besteed aan de ontvormbaarheid, zijn holle constructies met een optimale verhouding tussen stijfheid en gewicht mogelijk.
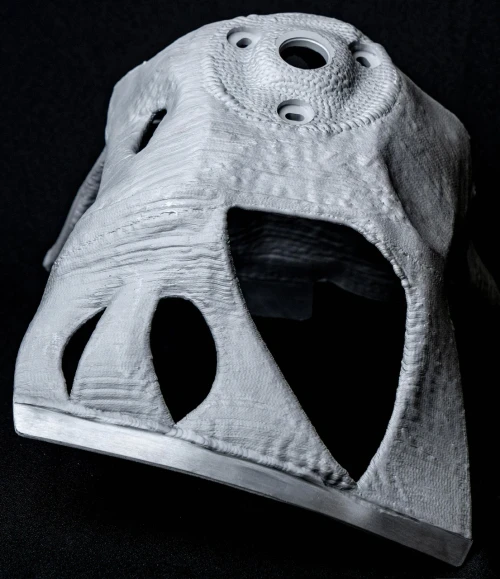
Dit betekent dat de componenten lichter en stijver kunnen zijn dan vergelijkbare spuitgietonderdelen die momenteel in serieproductie worden geproduceerd. Ze kunnen ook duurzamer worden geproduceerd dankzij lagere energiebehoeften en minder materiaalverspilling. In de toekomst is het plan om componenten die met behulp van het WAAM-proces zijn vervaardigd, te gebruiken in productievoertuigen van de BMW Group.
Door de grote breedte en hoogte van een enkele lasnaad kunnen componenten extreem snel worden geproduceerd met WAAM. In tegenstelling tot laserstraalsmelten, dat al wordt gebruikt in prototype- en kleine serieproductie bij de BMW Group, is WAAM met name geschikt voor grotere componenten. De typische wanddiktes zijn goed geschikt voor componenten in de carrosserie-, aandrijvings- en chassisgebieden. Echter, ook gereedschappen en apparaten kunnen worden vervaardigd met dit hightechproces, dat ook in de luchtvaartindustrie wordt gebruikt.
Sinds 2015 richten medewerkers van BMW Group zich op het WAAM-proces, ook wel opbouwlassen genoemd. Sinds 2021 is op de Additive Manufacturing Campus een WAAM-cel in gebruik voor de productie van testcomponenten. Een van deze voorbeeldtoepassingen is een veerpootondersteuning, die tijdens uitgebreide tests op de testbank wordt vergeleken met het serieproductiecomponent van aluminium spuitgietwerk.
In dit vroege stadium is al duidelijk dat het WAAM-proces kan leiden tot lagere emissies in het productieproces. Het lagere gewicht van de componenten, hun voordelige materiaalgebruikverhouding en de optie om hernieuwbare energie te gebruiken, betekent dat de componenten efficiënter kunnen worden geproduceerd.
—Jens Ertel, hoofd van BMW Additive Manufacturing
De volgende ontwikkelingsfase op weg naar serieproductie is het testen van componenten in het voertuig. Dit zal in de nabije toekomst gebeuren.
De bredere lasnaden in het WAAM-proces betekenen dat de oppervlakken van de componenten niet glad zijn, maar licht geribbeld en op kritische plekken afgewerkt moeten worden. BMW Group-ingenieurs konden echter aantonen dat WAAM-componenten gebruikt kunnen worden voor hoge belastingen, waaronder cyclische belastingen, zelfs zonder nabehandeling van het oppervlak.
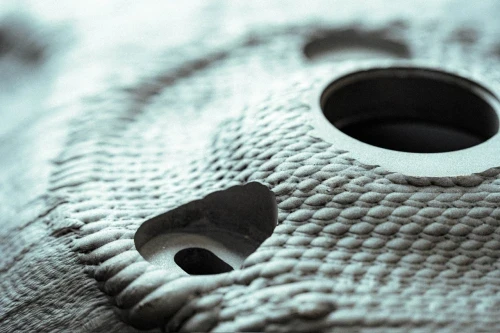
Geoptimaliseerde procesparameters zijn van cruciaal belang om duurzaamheid direct vanaf de productie te garanderen. Daarom is het belangrijk dat de combinatie van lasproces en robotpadplanning optimaal op elkaar is afgestemd.
Om optimaal gebruik te maken van de componenten die in het WAAM-proces worden geproduceerd, is de combinatie van het productieproces en een algemeen nieuw componentontwerp van het grootste belang. Om dit te bereiken, blijft de BMW Group het gebruik van generatief ontwerp versnellen. Hierbij gebruikt de computer algoritmen om geoptimaliseerde componenten te ontwerpen op basis van de specifieke vereisten.
Deze algoritmen worden ontwikkeld in nauwe samenwerking met interdisciplinaire teams en zijn deels geïnspireerd door evolutionaire processen in de natuur. Net als bij bionische structuren is de eerste stap om alleen het materiaal te gebruiken dat daadwerkelijk nodig is voor de topologie van het onderdeel, en tijdens de fine-tuning in de tweede stap wordt het onderdeel alleen versterkt waar nodig. Dit resulteert uiteindelijk in lichtere en stijvere onderdelen, evenals een grotere efficiëntie en verbeterde voertuigdynamiek.
Verschillende additieve productieprocessen concurreren niet per se met elkaar, maar moeten eerder als complementair worden beschouwd. Zo zal laserstraalsmelten nog steeds voordeliger zijn dan het WAAM-proces als het gaat om het hoogste niveau van detailresolutie. In termen van de mogelijke grootte van het onderdeel en de depositiesnelheid is draadboogadditieve productie echter superieur.
De BMW Group plant in eerste instantie een gecentraliseerde WAAM-productie van componenten in Oberschleißheim, in de toekomst is productie op andere locaties en het gebruik van de technologie door leveranciers ook mogelijk. Verder zou het zelfs denkbaar zijn om afzonderlijke componenten rechtstreeks op de assemblagelijn te produceren met behulp van dit proces en verschillende onderdelen te vervaardigen zonder nieuwe gereedschappen, gewoon door de software te wijzigen. Duurzaamheid kan ook verder worden verbeterd door het gebruik van gerecyclede metalen te vergroten.
Bron van Green Car-congres
Disclaimer: De hierboven vermelde informatie wordt verstrekt door greencarcongress.com, onafhankelijk van Cooig.com. Cooig.com geeft geen verklaringen en garanties met betrekking tot de kwaliteit en betrouwbaarheid van de verkoper en producten.