Banyak laser berada di pasaran hari ini, masing-masing dengan ciri, spesifikasi dan tahap penyepaduan mereka sendiri, menjadikan proses pemilihan sukar. Apabila memilih laser untuk pemprosesan bahan, adalah penting untuk memahami perbezaan dan faedah setiap pilihan.
Artikel ini memberi pembaca pemahaman tentang sistem laser, jenis laser biasa dan cara memilih sumber laser industri yang sesuai untuk pemprosesan bahan.
Jadual Kandungan
Pasaran laser industri global
Apakah sumber laser perindustrian?
Ciri yang perlu dipertimbangkan semasa memilih sumber laser
Garis bawah
Pasaran laser industri global
Pasaran laser industri dinilai pada USD 17.3 bilion pada 2021 dan dijangka berkembang pada kadar pertumbuhan tahunan kompaun (CAGR) sebanyak 7.2% untuk mencecah USD 34.8 bilion menjelang 2030. Pancaran cahaya dihasilkan oleh sistem laser industri menggunakan pelepasan terstimulasi untuk pelbagai tujuan dalam industri elektronik, automotif, perubatan dan lain-lain. Laser digunakan terutamanya untuk pematerian, pelabelan, ukiran, pemotongan, kimpalan dan penandaan.
Permintaan yang semakin meningkat untuk peningkatan kecekapan, produktiviti dan ketepatan telah menghasilkan pertumbuhan perindustrian laser. Tambahan pula, peningkatan permintaan untuk pemprosesan bahan dalam pelbagai sektor dan peralihan industri automotif kepada kenderaan elektrik akan memacu jualan pada masa hadapan.
Apakah sumber laser perindustrian?
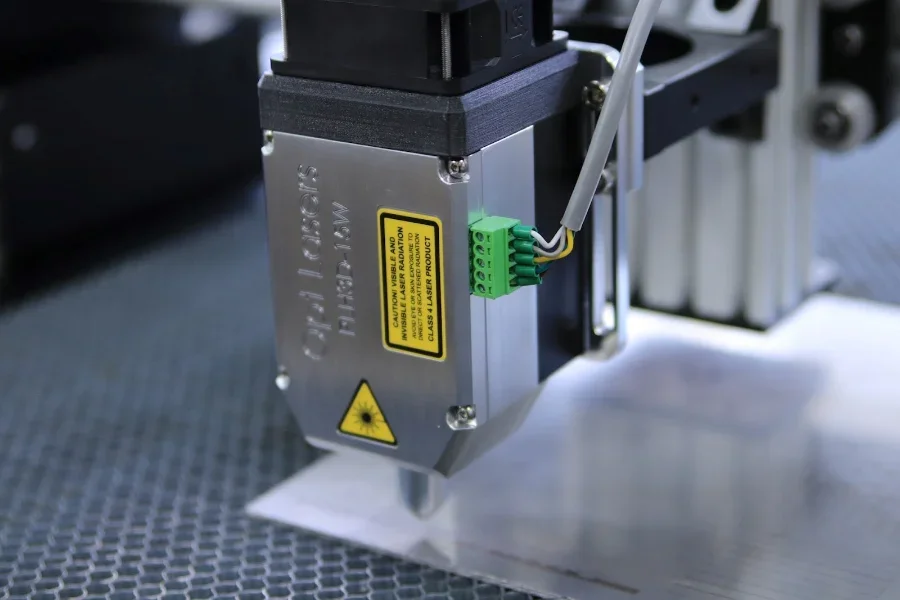
Laser mempunyai pelbagai komponen dan ciri yang menghasilkan pancaran cahaya yang sengit dan koheren melalui proses penguatan optik. Terdapat banyak jenis laser, masing-masing dengan tahap integrasi yang berbeza-beza. Semua ini laser, walau bagaimanapun, berkongsi set komponen asas.
Sumber tenaga untuk setiap laser mengarahkan cahaya ke dalam medium perolehan. Media keuntungan ini memancarkan panjang gelombang cahaya tertentu, dan resonator menguatkan keuntungan optik ini melalui cermin.
Sebelum masuk ke dalam spesifik sumber laser, mari kita lihat beberapa laser yang paling biasa:
Laser Keadaan Pepejal: Sebagai sumber utama keuntungan optik mereka, laser ini bergantung pada gelas pepejal atau kristal bercampur dengan unsur bumi lain. Biasanya, unsur campuran ini ialah erbium, thulium, kromium atau ytterbium. Keadaan pepejal yang paling biasa laser dalam aplikasi pemprosesan industri ialah delima dan Nd:YAG.
Laser Gas: Dengan menggunakan teknik yang dikenali sebagai penyongsangan populasi, arus elektrik disalurkan melalui gas dalam laser ini untuk menghasilkan cahaya. Karbon dioksida (CO2), argon, kripton, dan helium-neon adalah laser gas yang paling popular. CO2 laser adalah pilihan yang paling popular dan digunakan secara meluas untuk kimpalan, pemotongan dan penandaan laser.
Laser gentian: Laser gentian mempunyai lebih sempit dan lebih kecil laser rasuk daripada laser lain, menjadikannya lebih tepat dalam aplikasi pemprosesan bahan. Mereka mempunyai jejak yang kecil, cekap tenaga, dan mempunyai kos operasi dan penyelenggaraan yang rendah. Laser gentian digunakan secara meluas dalam aplikasi pembersihan, kimpalan, pemotongan dan penandaan.
Ciri yang perlu dipertimbangkan semasa memilih sumber laser
Langkah pertama ialah mengenal pasti jenis laser bergantung pada aplikasi laser. Selepas memutuskan jenis laser, seseorang mesti menentukan parameternya, termasuk kuasa, saiz, dan panjang gelombang rasuk dan kos penyelenggaraan.
Panjang gelombang pancaran laser
Adalah penting untuk mengkaji panjang gelombang pancaran laser untuk pemprosesan bahan kerana bahan yang berbeza mempunyai kadar penyerapan yang berbeza pada panjang gelombang yang berbeza. Satu peraturan yang diterima secara meluas ialah pancaran laser 1064 nm panjang gelombang laser Nd:YAG diserap dengan baik oleh keluli dan aluminium, manakala panjang gelombang 10600 nm laser pancaran laser karbon dioksida (CO2) diserap dengan baik oleh kain, plastik, kulit, kayu dan kertas.
Dua sumber laser yang paling biasa tersedia hari ini ialah CO2 dan serat. bergantung kepada unsur-unsur yang dicampur ke dalam gentian. Laser CO2 boleh menghasilkan pancaran laser pada 10600, 10300, atau 930 nm, bergantung pada komposisi gas. Adalah penting untuk memadankan panjang gelombang sumber laser dengan bahan yang akan diproses untuk memastikan operasi laser yang berkesan.
Kos penyelenggaraan
Pada masa lalu, laser CO2 tiub kaca dan laser Nd:YAG yang dipam lampu adalah popular, tetapi sumber pamnya, iaitu lampu arka atau tiub kaca berisi gas perlu diganti secara berkala. Setiap 500 hingga 1000 jam bekerja, pengguna terpaksa menghentikan mesin dan menggantikan tiub atau lampu. Tambahan pula, CO2 generasi lama laser memerlukan aliran gas yang berterusan melalui resonator, mengakibatkan kos operasi yang tinggi.
Walau bagaimanapun, terima kasih kepada teknologi canggih, serat laser, pilihan paling popular hari ini, mencakupi 80% bahagian pasaran, adalah bebas penyelenggaraan sepenuhnya. Mereka mempunyai hayat perkhidmatan yang panjang dan reka bentuk resonator laser yang unik di mana semua optik adalah sebahagian daripada kabel gentian optik berterusan yang cekap.
Kuasa dan saiz fokus
Pancaran laser boleh dihantar melalui optik pemfokus sambil dipulangkan pada panjang yang berbeza. Apabila rasuk bersentuhan dengan bahan kerja, ia mengecut dalam saiz, dengan berkesan memfokuskan sejumlah besar tenaga ke kawasan kecil. Walau bagaimanapun, output laser tidak boleh dikurangkan kepada saiz yang lebih kecil daripada panjang gelombangnya, begitu juga output berkualiti rendah menjana titik fokus berkualiti tinggi. Sebagai contoh, CO2 laser tidak boleh mengurangkan titik fokus kepada kurang daripada 10600 nm, memerlukan pancaran dan optik yang hampir sempurna untuk menyelesaikan tugas.
Oleh itu, walaupun saiz tempat adalah pertimbangan penting, ia tidak diperlukan untuk semua aplikasi, seperti pembersihan permukaan laser, kimpalan laser, dan pensinteran tangga, yang memerlukan saiz tempat yang lebih besar untuk memastikan prestasi.
Bahan pemprosesan laser
Oleh kerana bahan yang berbeza mempunyai kadar pemprosesan yang berbeza, sifat bahan mesti dipertimbangkan apabila memilih sumber laser yang betul. Bahan yang paling sesuai untuk penandaan, ukiran dan pemotongan laser CO2 termasuk plastik, buih, fabrik, getah, kertas, kaca, batu seramik, keluli, titanium, kayu dan komposit. Bahan dengan takat lebur yang sangat tinggi adalah tidak sesuai untuk laser CO2 di bawah 200 W.
Laser gentian sesuai untuk pelbagai bahan, termasuk asetal hitam, akrilik, PTFE, dan plastik yang mengandungi pengisi, pigmen, atau bahan tambahan penerima laser.
Cara operasi
Laser CW (gelombang berterusan).
Adalah penting untuk mengetahui sama ada laser berterusan atau berdenyut. Purata kuasa laser CW diukur dalam kW atau nW. Sebelum memilih sensor untuk CW laser, julat kuasa purata mesti ditentukan. Julat ini akan menentukan pilihan penderia yang tepat. Sebagai contoh, jika julat terlalu lebar, penderia kedua akan diperlukan. Oleh itu, memilih penderia dengan julat yang hampir dengan julat yang diperlukan—bukan pada hujung tinggi atau rendah, tetapi di tengah—boleh mengakibatkan bacaan rosak jika julat melebihi kedua-dua arah.
Untuk memilih sensor yang sesuai, masa pendedahan pancaran laser laser CW mesti dipertimbangkan. Jika hanya pengukuran berkala diperlukan, penderia dengan masa pendedahan yang cukup lama untuk memperoleh bacaan yang stabil, iaitu berpuluh-puluh saat, adalah mencukupi—sebaik-baiknya penderia yang lebih kecil dan lebih murah. Walau bagaimanapun, jika laser mesti didedahkan kepada penderia kuasa untuk tempoh yang lama, penderia yang lebih besar diperlukan untuk menghilangkan sebarang pembentukan haba yang boleh menjejaskan pengukuran.
Laser berdenyut
Seperti laser CW, keperluan julat tenaga untuk penderia mesti ditentukan. Pengguna mesti mengenal pasti denyutan sesaat laser (PPS) atau kadar nadi untuk menentukan sama ada penderia tenaga boleh digunakan untuk aplikasi tertentu. Kebanyakan penderia tenaga beroperasi pada frekuensi antara 1hz hingga 5 kHz, dengan penderia lanjutan beroperasi sehingga 25 kHz.
Faktor lain yang perlu dipertimbangkan dengan berdenyut laser ialah lebar nadi. Spesifikasi ini mempunyai kesan ketara pada ambang kerosakan sensor yang dipilih. Contohnya, jika lebar nadi terlalu pendek, ketumpatan tenaga mungkin melebihi penarafan sensor. Jika terlalu lama, litar sensor mungkin tidak mempunyai masa penyepaduan yang mencukupi, mengakibatkan operasi yang rosak.
Garis bawah
Memilih sumber laser yang betul adalah penting untuk memaksimumkan produktiviti dan meningkatkan ketepatan. Artikel ini memberikan beberapa cerapan tentang sumber dan ciri laser. melawat Cooig.com untuk menyemak peralatan laser terkini untuk aplikasi perindustrian.