2025 年、ボーリング マシン市場は、技術の進歩と産業需要の高まりにより活況を呈しています。この記事では、アプリケーションの特殊性、マシンの仕様、コストの考慮事項など、主要な選択要因の詳細な分析を提供します。プロのバイヤーが情報に基づいた決定を下し、最適なパフォーマンスと収益性を確保するための貴重なガイダンスを提供します。
目次:
-ボーリングマシン市場の概要
-ボーリングマシン市場の詳細な紹介と分析
-ボーリングマシンを選択する際の重要な要素
-ボーリングマシン技術の革新
-ボーリングマシン操作における環境配慮
-ボーリングマシン技術の将来動向
-まとめ
ボーリングマシン市場の概要
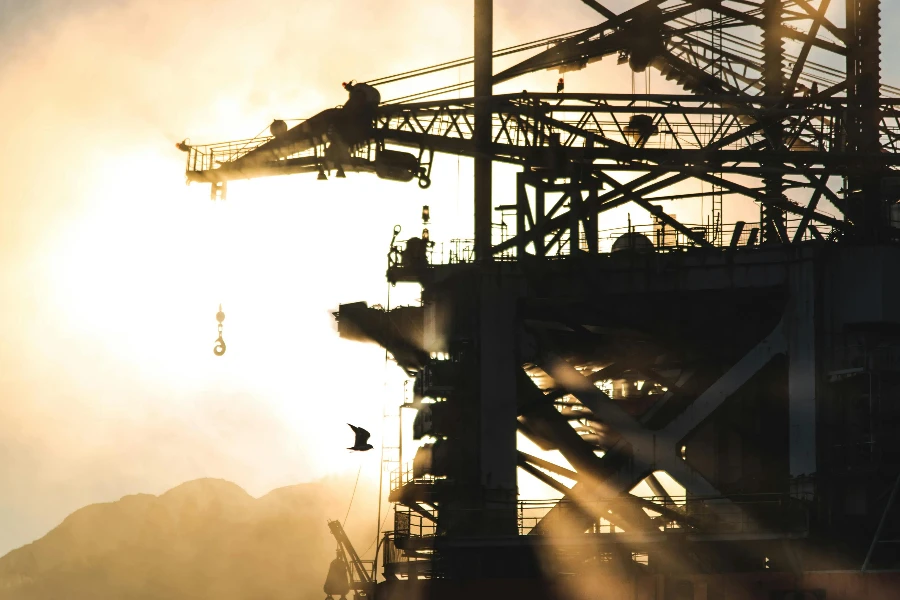
近年、ボーリングマシンの世界市場は著しい成長を遂げています。2023年の市場規模は約4.4億米ドルで、6.2年までに2030億米ドルに達し、CAGR 5.0%で成長すると予測されています。この成長は、製造技術の進歩と、自動車、航空宇宙、重機などの業界からの需要増加によって推進されています。輸送最終用途セグメントは最も大幅な成長が見込まれ、2.9年までにCAGR 2030%で5.3億米ドルに達し、一般機械セグメントはCAGR 4.4%で成長すると予想されています。
地域別に見ると、米国市場は1.2年に2023億米ドルに達すると推定されており、中国市場は7.6%という驚異的なCAGRで成長し、1.4年までに2030億米ドルに達すると予測されています。その他の重要な市場には、日本、カナダ、ドイツ、およびアジア太平洋地域全体があり、これらはすべて、ボーリングマシン市場全体の成長に貢献すると予想されています。
ボーリングマシン市場の詳細な紹介と分析
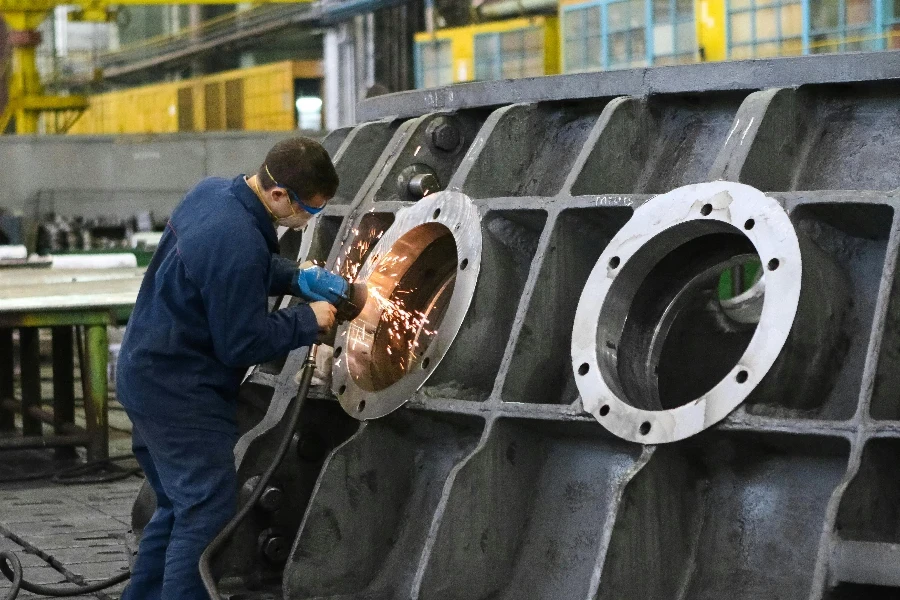
ボーリングマシンは精密加工に欠かせないもので、特に自動車、航空宇宙、重機など、高精度で滑らかな仕上げが求められる業界では欠かせません。これらのマシンは、事前にドリルで穴を開けたり鋳造したりした穴を高精度で拡大、仕上げできるように設計されており、直径、表面仕上げ、許容差が正確な仕様を満たすようにします。市場は、精密ボーリングと粗ボーリングのタイプに分かれており、それぞれが材料と切削条件に基づいて異なるニーズに対応しています。
技術の進歩により、ボーリングマシンの性能と汎用性が大幅に向上しました。多結晶ダイヤモンド (PCD) や立方晶窒化ホウ素 (CBN) などの高度なコーティングや刃先材料などの革新により、優れた耐摩耗性と長い工具寿命が実現しました。さらに、デジタル制御のボーリングヘッドにより、加工中にリアルタイムで調整できるため、比類のない精度が得られ、エラーが削減されます。予知保全のためのセンサー技術の統合により、加工プロセスがさらに最適化され、ダウンタイムが短縮されました。
こうした進歩にもかかわらず、ボーリングマシン市場は課題に直面しています。さまざまな材料にわたって精度を維持し、発熱を管理し、電子機器や医療機器などの業界で小型化の傾向に対処することは、継続的な課題です。メーカーは、これらの課題に対処するために、高度な冷却技術を研究し、より堅牢で多用途なツールを開発しています。製造におけるコスト圧力も、ダウンタイムと無駄を最小限に抑えながら高性能を発揮できる、より効率的なボーリングマシンの必要性を促しています。
ボーリングマシンを選択する際の重要な要素
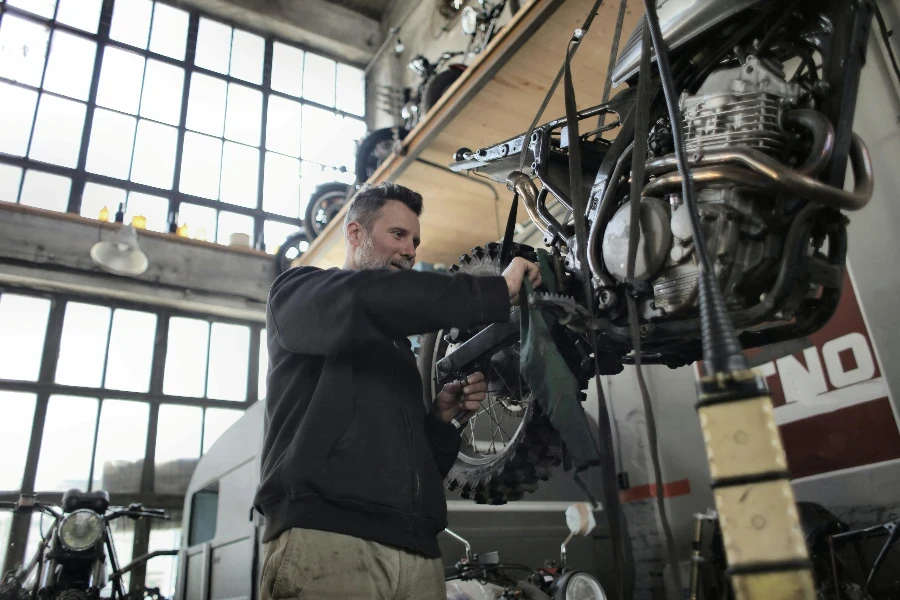
アプリケーションの特異性
ボーリングマシンを選択する際に最初に考慮すべき要素は、そのマシンが使用される特定のアプリケーションです。精密ボーリング、ジグボーリング、旋盤ボーリング、垂直ボーリング、水平ボーリングなど、さまざまなタスクを処理するために、さまざまなボーリングマシンが設計されています。たとえば、精密ボーリングマシンは高精度の円筒形内部表面を作成するのに理想的ですが、ジグボーリングマシンは正確な寸法と位置の穴を開けるのに適しています。タスクの特定の要件を理解することは、適切なマシンタイプを選択するのに役立ちます。
精密ボーリングマシンは、通常、シングルポイントの切削操作を使用して ±0.0001 インチ以内の精度を実現するため、内部ベアリング面の仕上げなどの高精度の作業に適しています。対照的に、より大きなワークピースを処理でき、フライス加工や穴あけなどの多機能機能を備えた水平ボーリングマシンは、汎用性が求められる高負荷アプリケーションに適しています。
ワークピースの複雑さ、必要な許容範囲、加工する材料は重要な考慮事項です。たとえば、ステンレス鋼などの硬度の高い材料の場合は、精度と効率を維持するために、超硬工具またはダイヤモンド工具を備えた機械が必要になる場合があります。
マシン仕様
ボーリング マシンの技術仕様は、アプリケーションの要求を満たすために不可欠です。主な仕様には、スピンドル速度、送り速度、切削速度、マシンのパワーなどがあります。スピンドル速度は毎分回転数 (RPM) で測定され、切削工具の回転速度を決定し、仕上げの品質と加工プロセスの効率に影響します。通常、仕上げが細かく、材料が硬い場合は、スピンドル速度を高くする必要があります。
送り速度は、通常、インチ/分 (IPM) で測定され、切削工具が材料に進入する速度を示します。スピンドル速度と送り速度の適切なバランスは、工具の摩耗を防ぎ、望ましい表面仕上げを実現するために不可欠です。切削速度、つまり工具の刃先がワークピースの表面に沿って移動する速度も、ボーリング プロセスの効率と品質を決定する上で重要な役割を果たします。
機械の電力要件は通常馬力 (HP) で指定され、材料除去率と加工対象材料の硬度に合わせる必要があります。たとえば、ステンレス鋼や鋳鉄などの材料を扱うボーリングマシンは単位電力要件が高いため、パフォーマンスを維持するためにより強力なモーターが必要になります。
公差と精度
許容差と精度は、特に高精度が求められる用途では、ボーリング マシンを選択する上で重要な要素です。ボーリング マシンの許容差とは、指定された寸法からの許容偏差を指し、マシンの種類や用途によって異なります。たとえば、精密ボーリング マシンは、±0.0001 インチという厳しい許容差を実現できるため、寸法精度が最も重要となる用途に適しています。
環境条件、工具の形状、機械部品と固定具の配置も、穴あけ加工の精度に影響します。切削液を使用すると、工具の温度を維持し、摩耗を減らし、切削速度と送り速度を上げて、精度を高めることができます。
さらに、機械、ワークピース、ツールのセットアップの剛性は、ボーリング プロセス中に精度を維持するために非常に重要です。堅牢な構造と高品質のコンポーネントを備えた機械では、精度を損なう可能性のあるたわみや振動が発生する可能性が低くなります。
材料の互換性
ボーリングマシンとさまざまな材料との互換性も、重要な考慮事項です。ボーリングツールは通常、高速度鋼 (HSS)、超硬合金、セラミック、またはダイヤモンドで作られており、それぞれ異なる材料と用途に適しています。たとえば、超硬合金とダイヤモンドのツールはステンレス鋼などの硬い材料の加工に適していますが、HSS ツールはアルミニウムや真鍮などの柔らかい材料に適しています。
硬度や加工性などの材料特性を理解することは、適切なボーリングマシンとツールを選択するために不可欠です。たとえば、鋳鉄やステンレス鋼などの硬度値の高い材料では、効率と精度を維持するために、耐摩耗性と切削速度の高いツールが必要です。
さらに、切削液の選択は、特に大量の熱を発生する材料を扱う場合には、加工プロセスに影響を与える可能性があります。切削液は、工具の摩耗を減らし、表面仕上げを改善し、切削速度を上げるのに役立つため、穴あけ加工では欠かせない要素です。
コストと予算
最後に、ボーリング マシンの購入にかかるコストと予算を考慮する必要があります。ボーリング マシンの価格は、種類、仕様、機能によって大きく異なります。自動化された CNC 制御のボーリング マシンは、精度と効率性が高く、手動または半自動のマシンよりも高価になる傾向があります。
ボーリング マシンへの投資は、予想される投資収益率 (ROI) と作業の特定のニーズに合わせて行う必要があります。小規模または頻度の低い作業の場合は、基本的な機能を備えた低コストのマシンで十分です。ただし、大量生産や高精度が求められるアプリケーションの場合は、より高度で高価なマシンに投資することで、効率性の向上とダウンタイムの短縮により長期的なコスト削減を実現できます。
メンテナンス費用、ツールの交換、エネルギー消費も全体の予算に考慮する必要があります。エネルギー効率が高く、メンテナンス要件が低いマシンは、長期的に運用コストを大幅に削減できます。
ボーリングマシン技術の革新
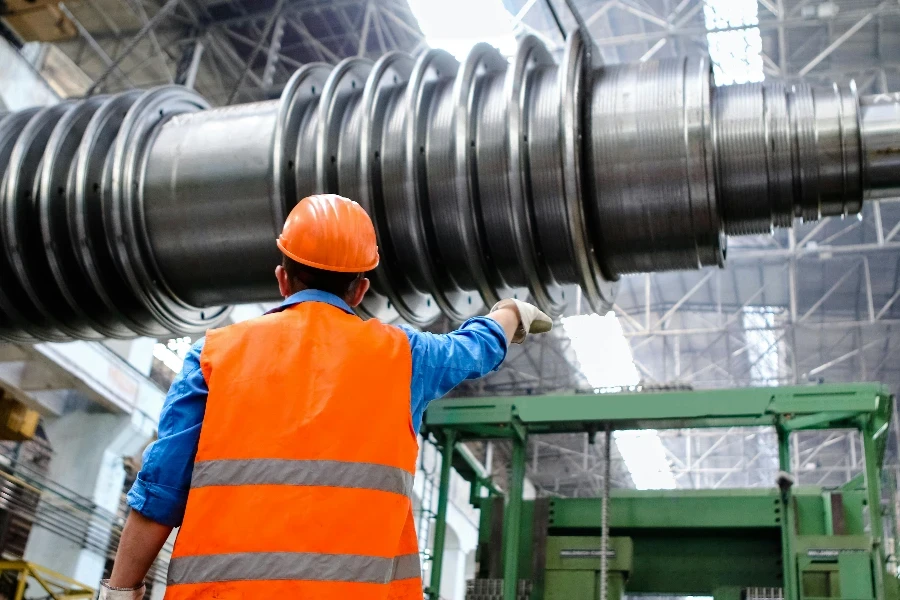
CNCの統合
ボーリング マシンにコンピュータ数値制御 (CNC) 技術を統合することで、精度、効率、自動化が向上し、業界に革命が起こりました。CNC ボーリング マシンは G コードを使用してプログラムされ、切削工具の動き、速度、送り速度を正確に制御できます。この技術により、複雑で反復的なタスクを最小限の人的介入で実行できるため、エラーの可能性が減り、生産性が向上します。
CNC ボーリング マシンには、自動ツール チェンジャーなどの高度な機能が搭載されており、手動操作なしで 1 回の操作で複数のツールを使用できます。この機能は、荒加工や仕上げ加工など、ボーリング プロセスのさまざまな段階で異なる切削ツールを必要とするアプリケーションに特に役立ちます。
さらに、CNC 技術により、シミュレーション ソフトウェアを使用して実際の機械加工の前にボーリング プロセスをモデル化し、潜在的な問題を特定してパラメータを最適化し、効率と精度を向上させることができます。この予測機能により、セットアップ時間が短縮され、材料の無駄が最小限に抑えられ、コスト削減と環境の持続可能性に貢献します。
先端工具材料
高度な工具材料の開発は、ボーリング マシンの性能と耐久性に大きな影響を与えています。多結晶ダイヤモンド (PCD) や立方晶窒化ホウ素 (CBN) などの高性能材料は、従来の HSS や超硬工具に比べて優れた硬度と耐摩耗性を備えています。これらの材料により、特に硬くて研磨性のある材料を加工する場合、切削速度の向上、工具寿命の延長、表面仕上げの改善が可能になります。
PCD ツールは、アルミニウムや複合材などの非鉄材料に最適で、高精度と長いツール寿命を実現します。一方、CBN ツールは、硬化鋼や鋳鉄などの鉄材料に適しており、優れた熱安定性と耐摩耗性を備えています。
窒化チタン (TiN) や酸化アルミニウム (Al2O3) などの高度なコーティングを使用すると、切削プロセス中の摩擦と熱の発生が低減され、工具の性能がさらに向上します。これらのコーティングにより、切りくずの排出が改善され、工具の摩耗が軽減され、切削速度が向上するため、生産性が向上し、コストが節約されます。
オートメーションとロボティクス
自動化とロボット工学は、ボーリングマシン業界でますます重要な役割を果たしており、効率、精度、安全性を高めています。自動化されたボーリングマシンは、人間の介入を最小限に抑えて複雑なタスクを実行できるため、人件費とエラーのリスクが軽減されます。ロボット システムをボーリングマシンに統合すると、材料の取り扱い、ツールの交換、品質検査を自動化できるため、製造プロセスがさらに合理化されます。
たとえば、ロボット アームはワークピースの積み下ろし、機械への正確な配置、バリ取りや洗浄などの二次作業を行うことができます。このレベルの自動化により、生産性が向上するだけでなく、重くて危険な材料を手作業で取り扱う必要性が減るため、職場の安全性も向上します。
ロボット システムには、高度なセンサーと機械学習アルゴリズムを装備して、穴あけプロセスをリアルタイムで監視し、異常を検出して調整を行い、パフォーマンスを最適化することもできます。この機能により、機械加工プロセスの全体的な効率と信頼性が向上し、ダウンタイムとメンテナンス コストが削減されます。
掘削機操作における環境配慮
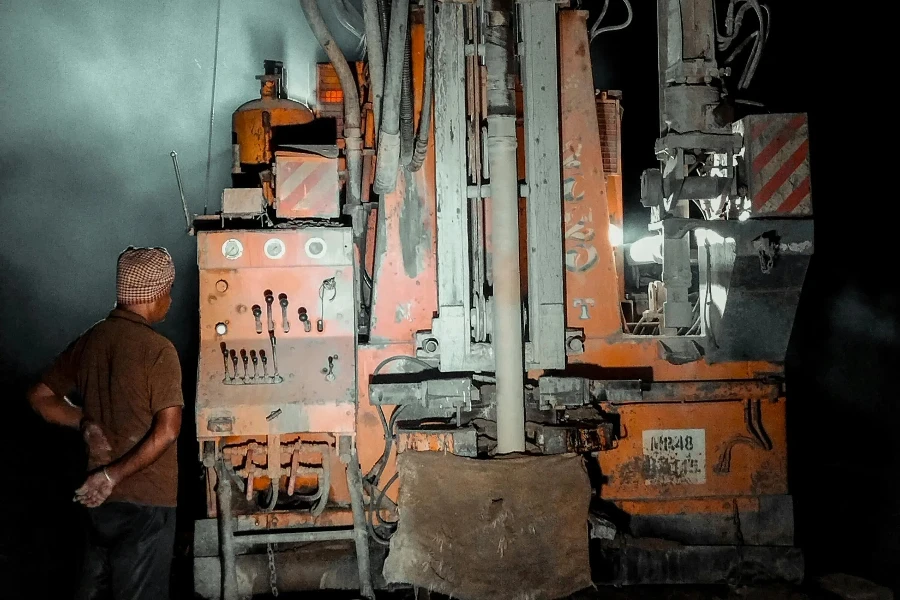
エネルギー効率
エネルギー効率は、運用コストと環境への影響を削減する必要性から、現代の掘削機の運用において重要な考慮事項となっています。高効率電気モーターや可変周波数ドライブ (VFD) などのモーター技術の進歩により、掘削機のエネルギー効率は大幅に向上しました。これらの技術により、モーターの速度とトルクを正確に制御できるようになり、エネルギー消費が削減され、パフォーマンスが最適化されます。
さらに、LED 照明や低電力電子機器などのエネルギー効率の高いコンポーネントの使用は、全体的なエネルギー節約にさらに貢献します。エネルギー管理システムを導入してエネルギー使用量をリアルタイムで監視および制御すると、非効率性を特定して是正措置を実施できるため、大幅なコスト削減と二酸化炭素排出量の削減につながります。
廃棄物削減
廃棄物の削減は、持続可能なボーリングマシン運用のもう 1 つの重要な側面です。材料の効率的な利用と最適化された加工プロセスにより、材料の無駄を最小限に抑え、製造による環境への影響を軽減できます。高度なシミュレーション ソフトウェアと CNC テクノロジにより、ボーリング プロセスを正確に制御できるため、スクラップ率が低減し、材料の収率が向上します。
切削液、チップ、その他の廃棄物をリサイクルして再利用することも、廃棄物の削減に貢献します。切削液の管理とチップのリサイクルのための閉ループ システムを実装すると、廃棄物処理コストを最小限に抑え、機械加工作業による環境への影響を軽減できます。
排出制御
安全で環境に優しい職場環境を維持するためには、掘削機の作業による排出物を制御することが不可欠です。ミストコレクターやエアスクラバーなどの高度な濾過システムを使用すると、オイルミスト、冷却剤蒸気、粒子状物質などの空気中の汚染物質を効果的に捕捉して除去できます。これらのシステムは、空気の質を維持し、環境規制に準拠して、作業員と周辺地域の健康を守るのに役立ちます。
さらに、環境に優しい切削液と潤滑剤を選択すると、有害な排出物を減らし、職場の安全性を向上させることができます。水性および生分解性の切削液は、従来の油性流体よりも安全で持続可能な代替品であり、機械加工作業による環境への影響を最小限に抑えます。
ボーリングマシン技術の将来動向
スマートマニュファクチャリング
インダストリー 4.0 とスマート製造の台頭により、接続性、データ分析、自動化の向上により効率と精度が向上し、ボーリング マシン業界は変革を遂げようとしています。センサーと IoT 接続を備えたスマート ボーリング マシンは、データをリアルタイムで収集して分析できるため、マシンのパフォーマンス、ツールの摩耗、プロセス パラメータに関する貴重な情報が得られます。
このデータ駆動型のアプローチにより、予測メンテナンスが可能になり、ダウンタイムが短縮され、機械やツールの寿命が延びます。機械の故障につながる前に潜在的な問題を特定することで、メーカーはメンテナンス スケジュールを最適化し、予期しない故障のリスクを軽減して、全体的な生産性とコスト効率を向上させることができます。
積層造形の統合
積層造形 (AM) と従来のボーリング プロセスを統合することで、複雑な部品の製造とカスタマイズに新たな可能性が生まれます。積層造形と切削造形を組み合わせたハイブリッド マシンでは、従来の機械加工だけでは実現が困難または不可能な複雑な形状や内部機能を製造できます。
積層造形により、ほぼネットシェイプの部品を作成できるため、材料の無駄が減り、大規模な機械加工の必要性が最小限に抑えられます。AM と精密ボーリングを組み合わせることで、メーカーは複雑な部品に高品質の仕上げと厳しい公差を実現でき、アプリケーションの範囲が広がり、全体的な効率が向上します。
持続可能性と循環経済
持続可能性と循環型経済は製造業においてますます重要になってきており、より環境に優しいボーリングマシン技術の開発を促進しています。メーカーは、エネルギー消費の削減、廃棄物の最小化、材料の再利用とリサイクルの促進に重点を置いています。
再生可能エネルギー源の使用、切削液管理のための閉ループシステムの実装、分解とリサイクルが容易な機械の設計など、持続可能な慣行の採用は、掘削機の運用による環境への影響を軽減する上で重要な役割を果たします。
まとめると、適切なボーリング マシンを選択するには、アプリケーションの特殊性、マシンの仕様、許容範囲と精度、材料の適合性、コストを慎重に考慮する必要があります。CNC 統合、高度なツール材料、自動化などの技術の進歩により、効率、精度、持続可能性が向上しています。エネルギー効率、廃棄物の削減、排出制御などの環境への配慮は、現代のボーリング マシンの運用においてますます重要になっています。スマート製造、積層造形統合、持続可能性などの将来のトレンドは、引き続き業界を形成し、メーカーに新たな可能性と課題をもたらします。